General Information
Default Menu Location: Transaction >> Production >> Production WO Master
Screen Name: WOMAST
Function: The Assign Serial/Lots tab allows you to assign serialized or lot controlled inventory to a line item on the PWO.
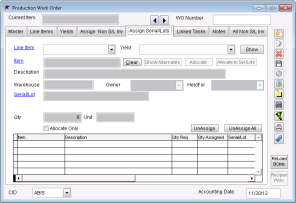 PWO - Assign S/L Tab Click here for a screenshot |
Fields/Filters
The grid on the bottom of the screen displays items from the Bill of Material. It will also display any additional items that have been allocated or assigned.
Lines highlighted in red have not met their required quantity (Qty Req) per the Bill of Material.
Lines highlighted in green have met or exceeded their required quantity.
There are eight tabs on the Production Work Order screen.
Links to the other seven tabs may be found here:
Line Item: The selected item from the Line Items tab.
Yield: The selected yield for the Line Item. This field can be used to assign serial/lot inventory to a specific yield (if there is more than one yield for the line item).
Item: The input Item Code.
Description: The input Item Description.
Whse: The warehouse the item is being taken from.
Owner: The Inventory Owner.
Held For: The Inventory Holder.
Serial/Lot: The serial or lot number of the item.
This number must match a current serial/lot in the Warehouse/Owner/Held For combination.
Bin: The bin number the serial/lot is being taken from.
This field will only be visible if the USEBINS setup option is turned on.Qty: The quantity that is being used.
Unit: The Unit of Measure. This will always be the item's Stock Unit.
Clear: Click this button to clear the Item, Description, and Qty fields when editing.
Show Alternates: Click this button to display alternate items for the input item.
Alternate items may be set up in the
Bill of Material screen.
Allocate Only: Check this box to allocate new input items instead of assigning them. They will appear in red as if they were on the original bill of material.
Assign Inventory Logic
Assigning inventory makes a green line and removes the assigned material from inventory and places into WIP. All inventory and accounting transactions are listed below. Each of these transactions happens at the time the inventory is assigned.
Accounting Transactions1.
The Inventory account of the Input item(s) is credited.The Average Cost of the item according to Owner/Held For/Warehouse is used.
2.
The Work in Process account of the the Input item is debited.The same cost as described in #1 is used.
Inventory Transactions1. Input items are taken out of stock and placed into WIP.
All stock input items are taken out of stock and placed into WIP when they are assigned to the production work order.
Allocate Inventory Logic
Users may Allocate material instead of assigning it to a production work order. Allocating material reserves the material to be used on the work order rather than actually taking the material out of inventory. Allocating material allows users to pre-select the material they wish used on the job.
To allocate materials, users will select a lot to allocate and make sure the "Allocate Only" check box is selected when the material is saved. This will highlight the allocated material as a yellow line.
Other options to allocate material is to use the "SO Allocate" button, which will allow users to choose the lot(s) they want to use to allocate.
To remove the allocated material, select the line from the grid and hit the "Remove Allocation" button.