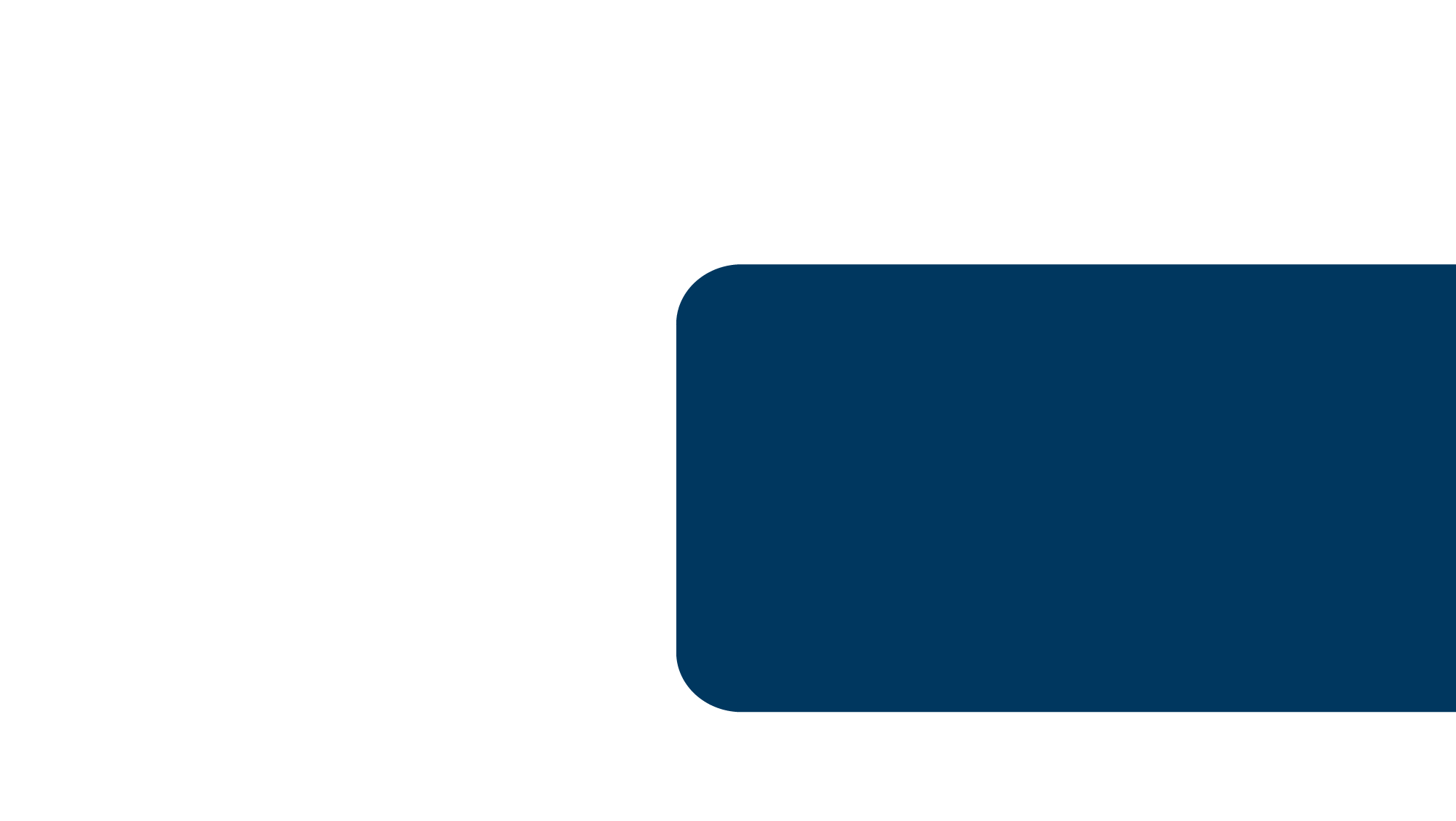
We're In The Business
Of Growing Your Business
Don't see what you do listed here?
Reach Out To Us
and see how Adjutant fits into your business!
• Job Shop Manufacturing
• Repetitive Manufacturing
• Discrete Manufacturing
• Batch Process Manufacturing
• Continuous Process Manufacturing
• Machining
• Joining
• Forming
• Casting

We're In The Business
Of Growing Your Business
• Machining
• Joining
• Forming
• Casting
• Job Shop Manufacturing
• Repetitive Manufacturing
• Discrete Manufacturing
• Batch Process Manufacturing
• Continuous Process Manufacturing
Don't see what you do listed here?
Reach Out To Us
and see how Adjutant fits into your business!
Features For Your Industry
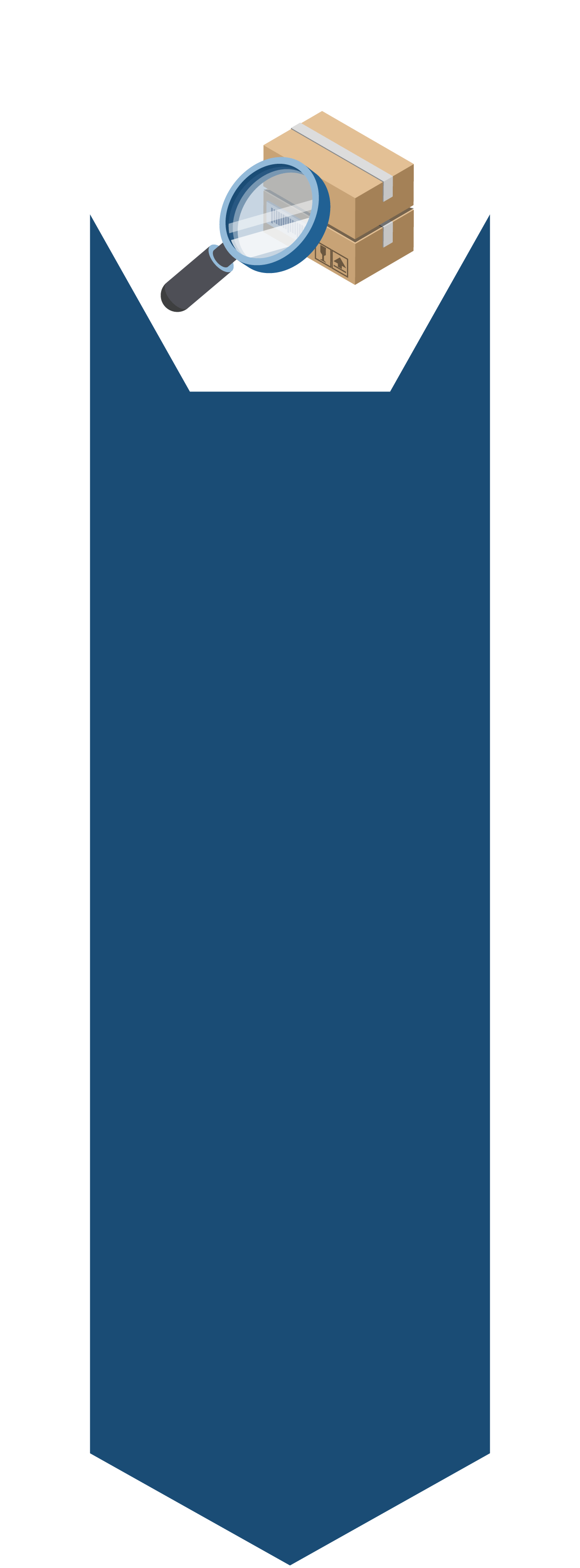
ASSET MANAGEMENT
Adjutant’s Asset Management Tracking module manages the complete asset lifecycle, and integrates with Purchasing, Sales, Production, and Service Orders. Depreciation tables, integrated GL posting, and reporting are available for all assets. Assets can be used as resources on service orders and projects and can be utilized with remote location tracking including GPS-compatible mapping.
This module allows the user to enter and track assets in the system based on location, entry date, department, RFID, and other metrics. Controls and attributes can be assigned based on asset type, and assets are categorized based on unique inventory codes. Assets can even be integrated with other machinery or programs through Adjutant to further streamline the tracking process.
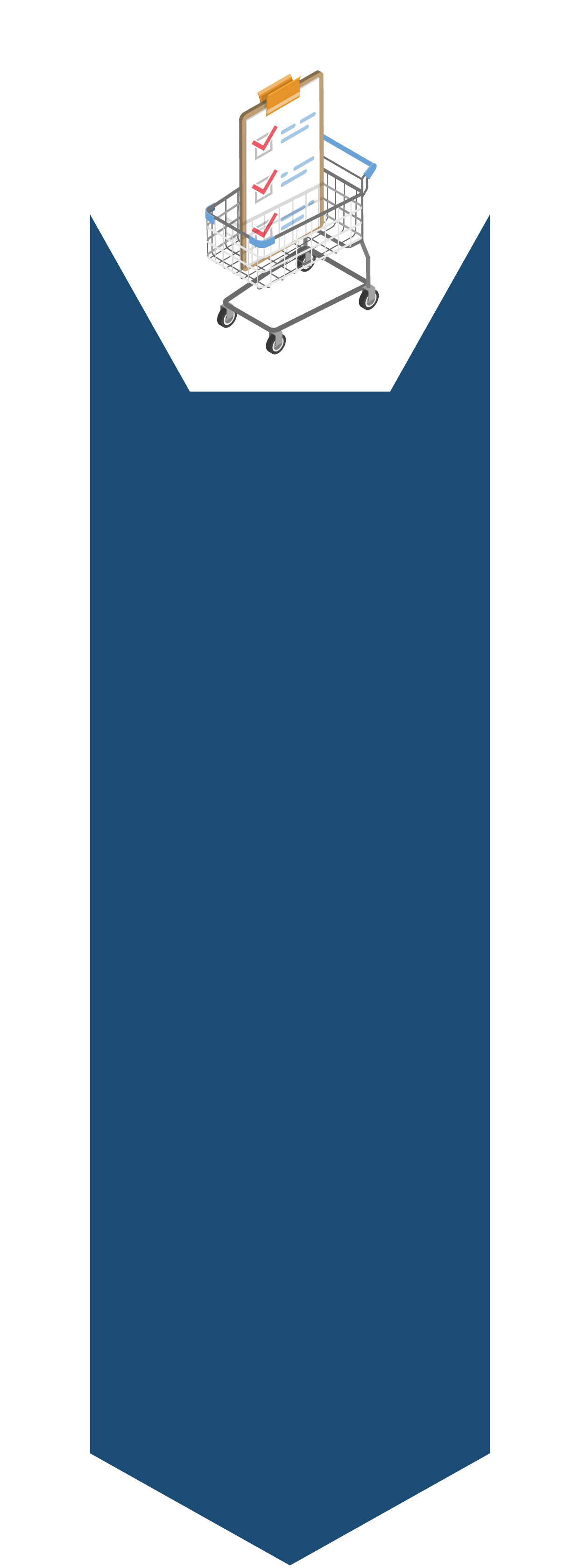
BILL OF MATERIAL
Adjutant’s Bill of Material defines the relationship between a manufactured or processed item and all its component materials or tasks required to assemble. It can maintain unlimited levels of material specifications and works equally well for manufacturing and process industries.
The Bill of Material allows both physical items and standard tasks to be components in the production process. This allows for tracking both material and labor on the same BOM.
To accommodate real-world manufacturing, Adjutant includes extensive support for substitution of alternate items at the time of processing. Alternate items can have different requirements for quantities than the normal bill. (Ex: a build may take 5 1-in. screws or 4 1.5-in screws.)
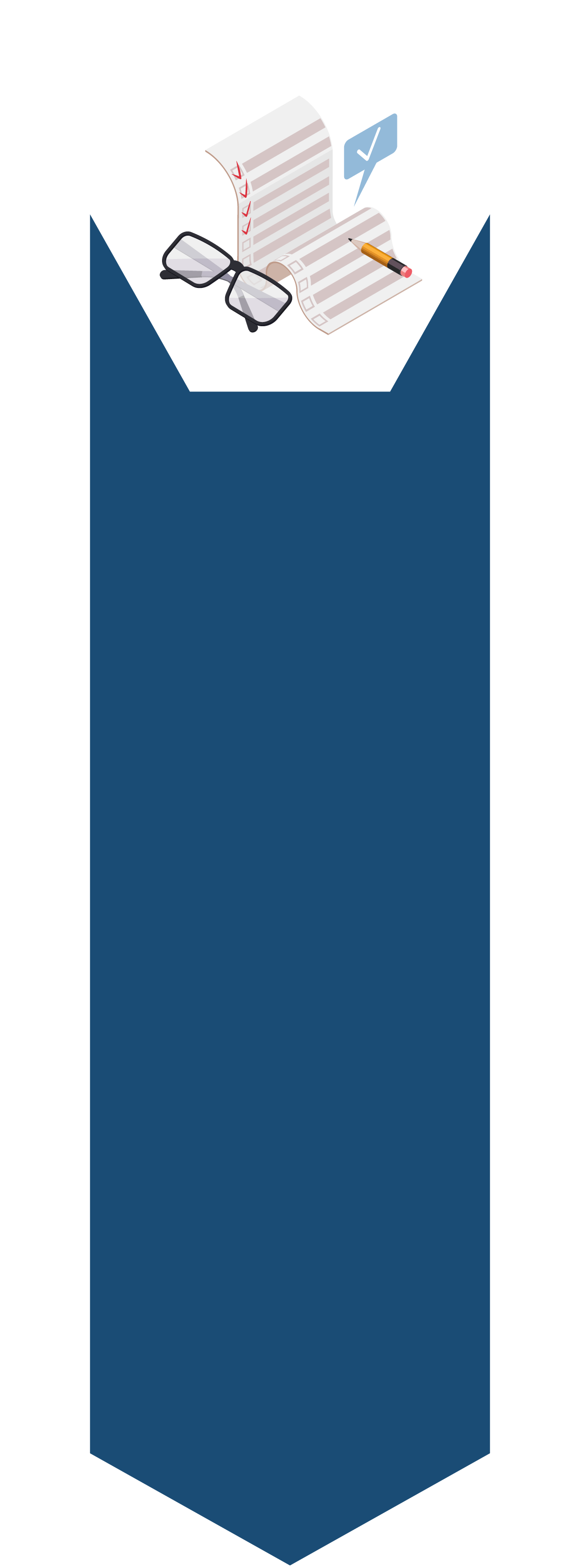
MRP
The Material Requirement Planning (MRP) system is tightly integrated with Adjutant’s Customer Orders, Inventory, Sales Analysis, Purchasing, and Manufacturing modules. It is sensitive to company- and plant-specific criteria and analyzes the existing stock status of all raw materials and finished goods. Users can determine precisely when and how much material should be purchased or manufactured based on a time-phased analysis of sales orders, production orders, purchase orders, current inventory levels, and forecasts. View demand analysis daily, weekly, or monthly.
Complete pegging is supported, allowing the user to drill-down to the critical data that makes up a customer order and its related commitments.
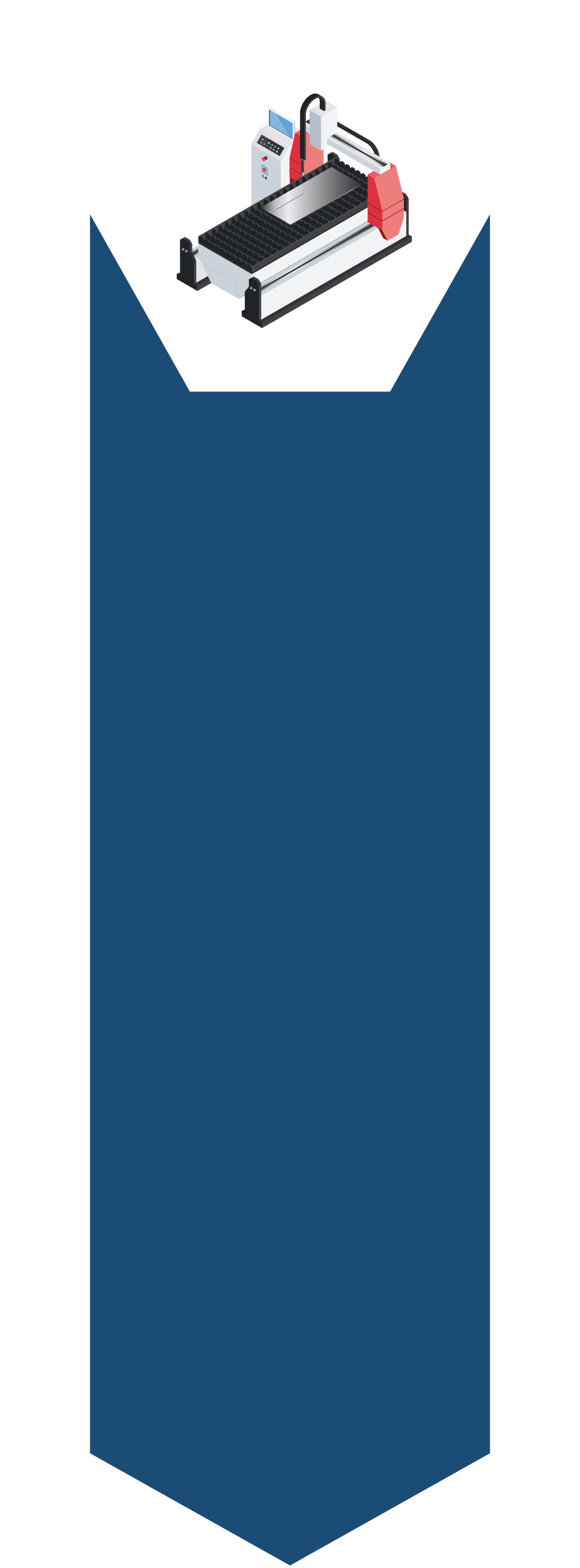
PRODUCTION & MANUFACTURING
Adjutant’s Production features automate manufacturing and assembly from start to finish. Production work orders list every part needed for assembly or fabrication based on a Bill of Materials with allocations and detailed inventory tracking. Scheduling and work order generation happens with a push of the button from the sales order.
Production Work Order Routing facilitates the scheduling and management of a production work-flow environment, managing the execution of a predetermined schedule and automatically updating the schedule based on set triggers. Inventory accounting is immediately created, both for work-in-process allocation and final assembly. Detailed reports offer a complete accounting picture of raw material costs and finished good inventory value.
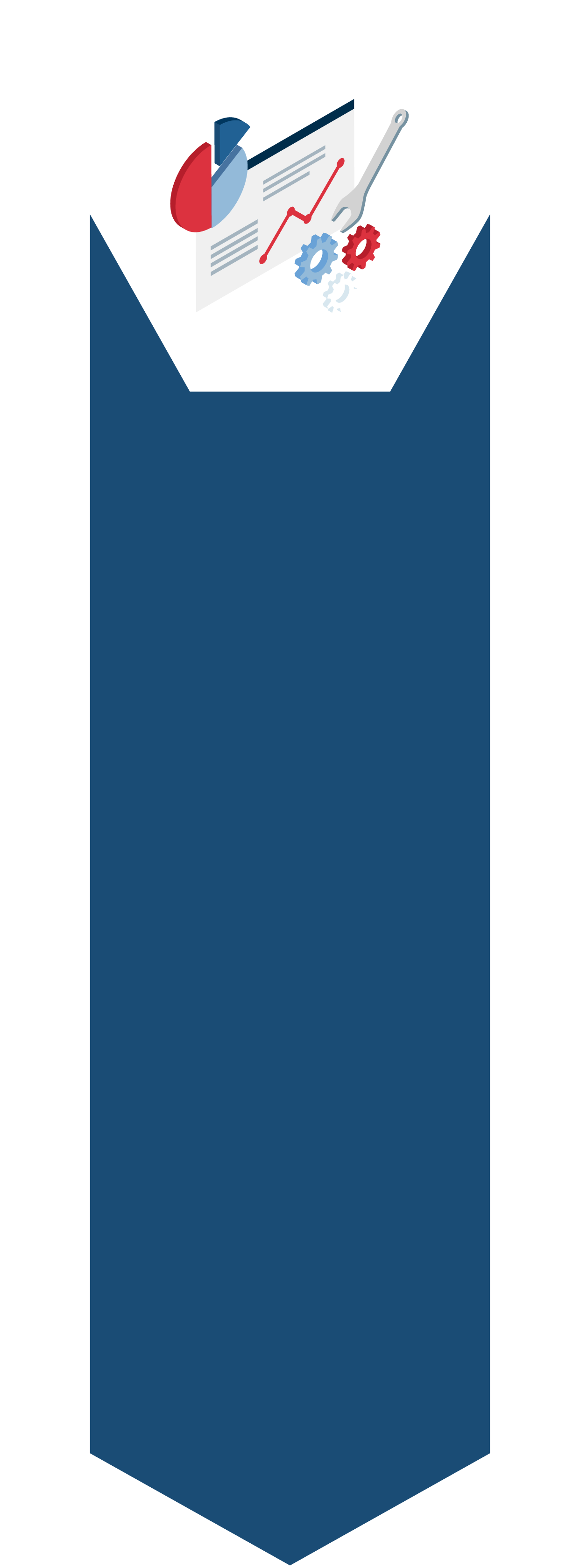
SHOP FLOOR CONTROL
The Shop Floor Control module in Adjutant is a powerful yet easy-to-use tool that gives you the ability to efficiently schedule your shop floor and utilize all your work centers to their most productive capacity. Access up-to-date information on the current activity in your shop, including job details and the order work needs to be performed in. Before committing to a schedule, quickly identify potential bottlenecks on the shop floor and compare the work committed against the shop floor’s ability to perform the work.
With Adjutant, you always know the status of a job on the floor - including production status, cost variables, and shipping schedules.
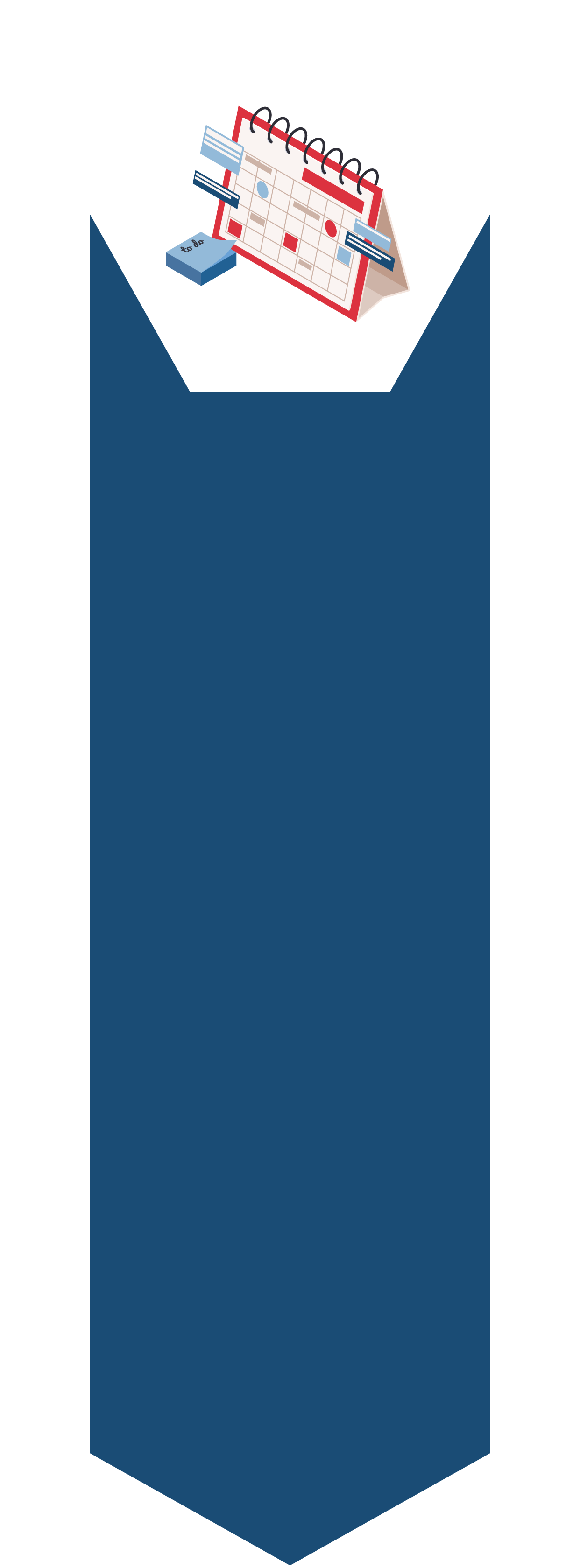
SHOP FLOOR ROUTING
Working in conjunction with the Production and Bill of Material modules, Adjutant’s Production Work Order Routing facilitates the scheduling and management of a production work-flow environment. It manages the execution of a predetermined schedule and automatically updates the schedule based on a combination of variables. Increase productivity, decrease costs, and receive better labor and material projections with the Routing module.
The Production Scheduling tool offers a way to manage all the production work orders in your shop with an on-screen display based on the production plant and due date. From one screen, you can quickly find orders using common filters - and reschedule, reprint, or change order details with just a few clicks.
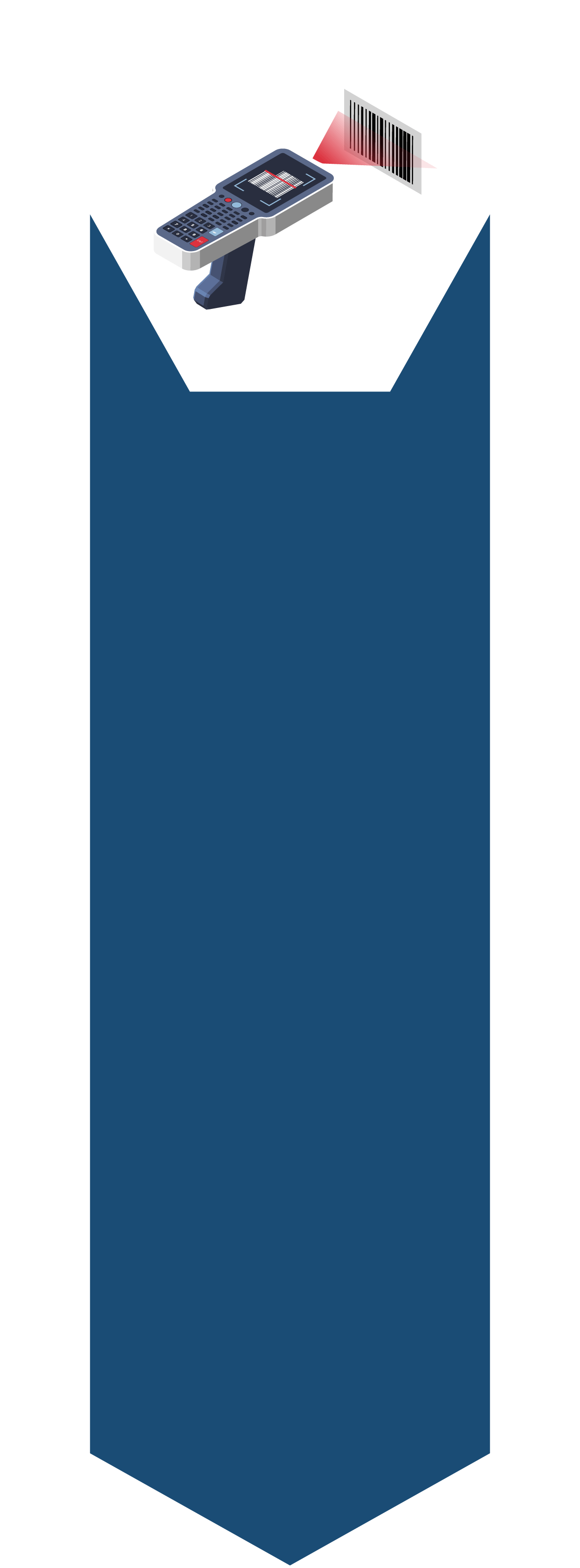
WIRELESS WMS
Adjutant’s Wireless Warehouse Management System (WMS) utilizes incredibly stable wireless barcode technology and provides comprehensive, real-time visibility of every activity in your warehouse. This module handles receiving, put-away, picking, packing, and complete inventory management.
The WMS integrates with Adjutant’s Inventory Management system to allow inventory cycle counts to be created and sent directly to certain scanners so that the counters are assigned to exactly the inventory locations or items that they need to cover. The prompts on the scanners walk employees through the process, leaving little room for error. Scanners can also be used to check inventory levels, manage inventory locations, and produce inventory labels on-the-fly.
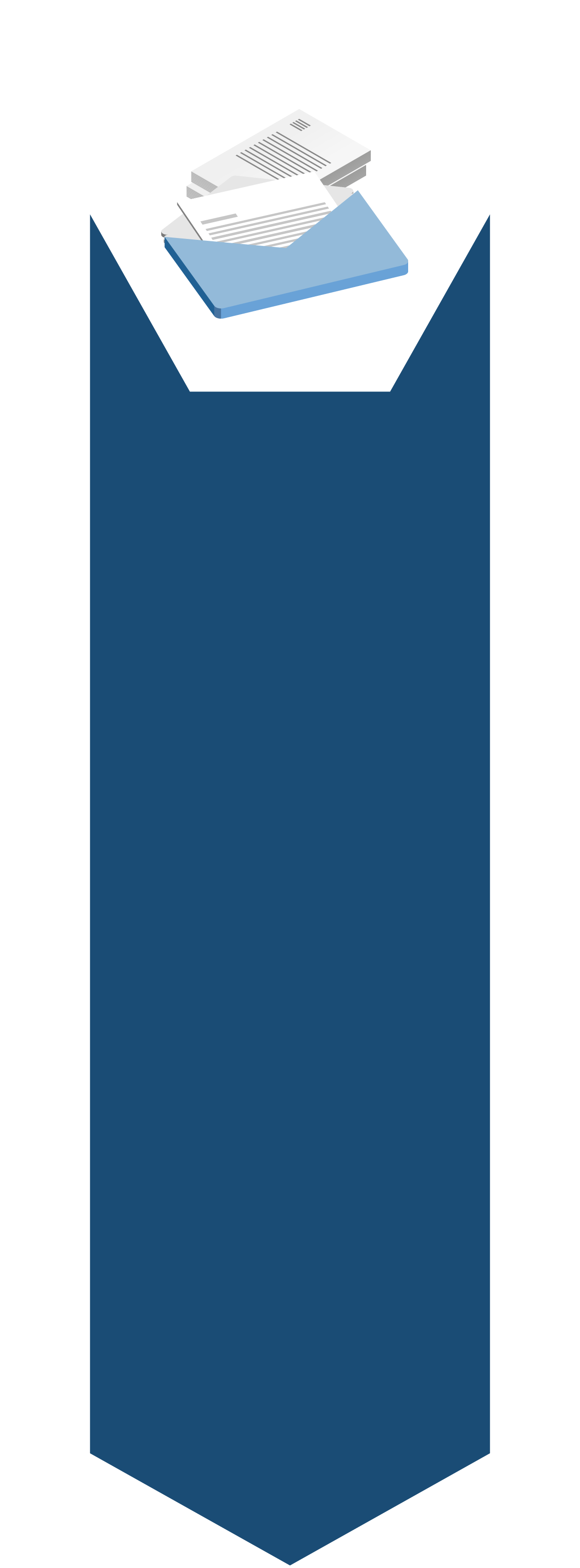
WORK ORDER MANAGEMENT
Adjutant’s Work Order Management module enables you to control your workflow by utilizing an efficient methodology to issue and assign work orders. It is the perfect tool to increase the performance of your in-house and mobile workforce.
Plan predetermined recurring tasks for preventative maintenance schedules or create and assign them on-the-fly as needed. Wireless connectivity gives you real-time visibility of mobile work-in-progress information and allows you to make better dispatch decisions. Seamless integration with other Adjutant modules gives your entire workforce immediate access to client and site information, contractual obligations, project information, and so much more!
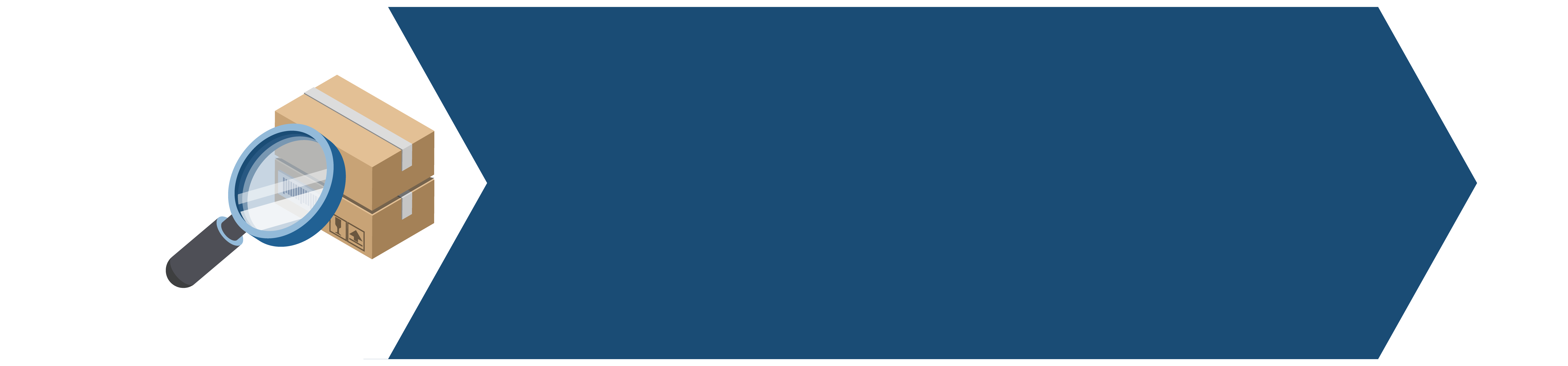
ASSET MANAGEMENT TRACKING
Adjutant’s Asset Management Tracking module manages the complete asset lifecycle, and integrates with Purchasing, Sales, Production, and Service Orders. Depreciation tables, integrated GL posting, and reporting are available for all assets. Assets can be used as resources on service orders and projects and can be utilized with remote location tracking including GPS-compatible mapping.
This module allows the user to enter and track assets in the system based on location, entry date, department, RFID, and other metrics. Controls and attributes can be assigned based on asset type, and assets are categorized based on unique inventory codes. Assets can even be integrated with other machinery or programs through Adjutant to further streamline the tracking process.
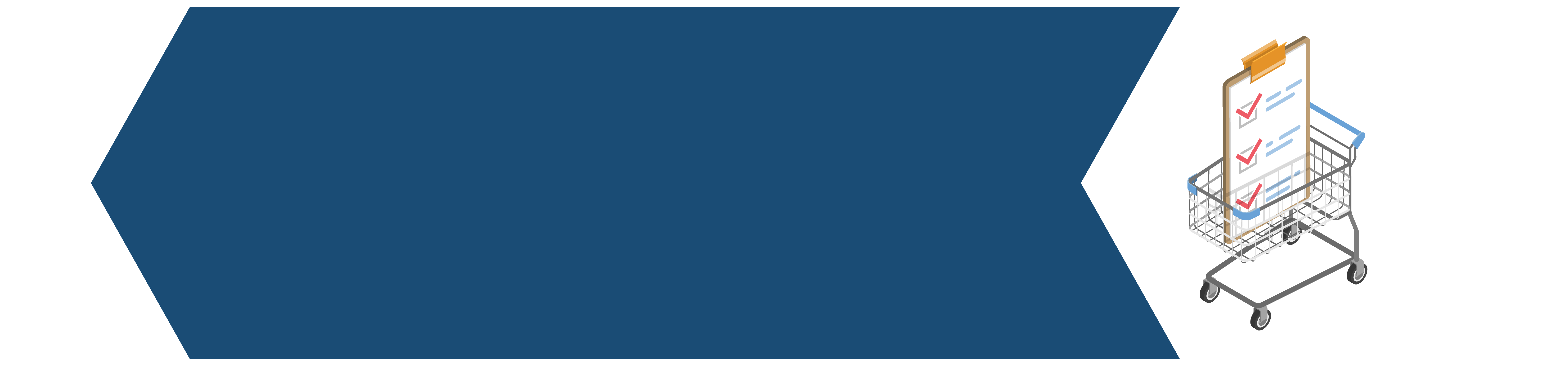
BILL OF MATERIAL
Adjutant’s Bill of Material defines the relationship between a manufactured or processed item and all its component materials or tasks required to assemble. It can maintain unlimited levels of material specifications and works equally well for manufacturing and process industries.
The Bill of Material allows both physical items and standard tasks to be components in the production process. This allows for tracking both material and labor on the same BOM.
To accommodate real-world manufacturing, Adjutant includes extensive support for substitution of alternate items at the time of processing. Alternate items can have different requirements for quantities than the normal bill. (Ex: a build may take 5 1-in. screws or 4 1.5-in screws.)
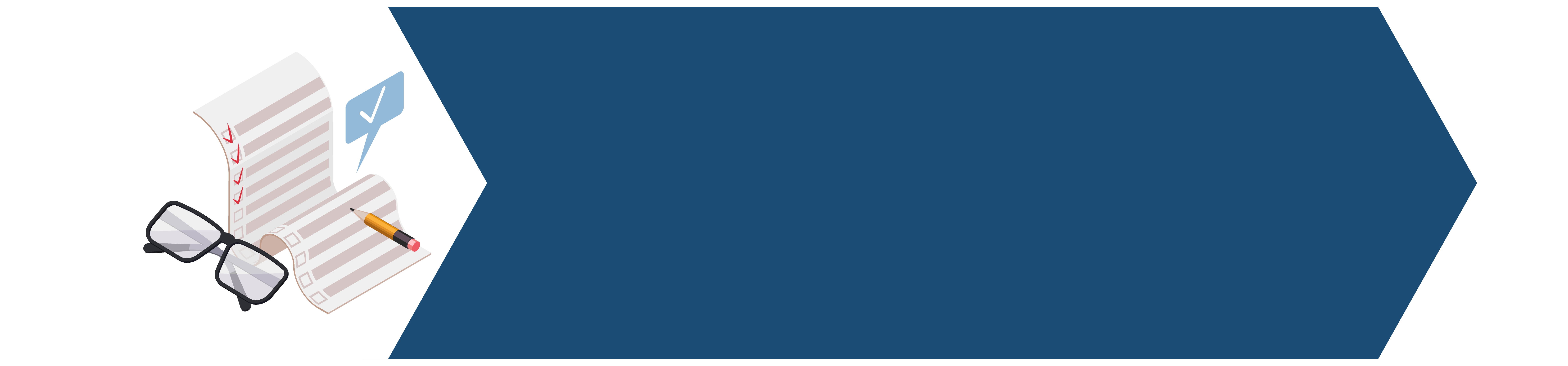
MATERIAL REQUIREMENTS PLANNING
The Material Requirement Planning (MRP) system is tightly integrated with Adjutant’s Customer Orders, Inventory, Sales Analysis, Purchasing, and Manufacturing modules. It is sensitive to company- and plant-specific criteria and analyzes the existing stock status of all raw materials and finished goods. Users can determine precisely when and how much material should be purchased or manufactured based on a time-phased analysis of sales orders, production orders, purchase orders, current inventory levels, and forecasts. View demand analysis daily, weekly, or monthly.
Complete pegging is supported, allowing the user to drill-down to the critical data that makes up a customer order and its related commitments.
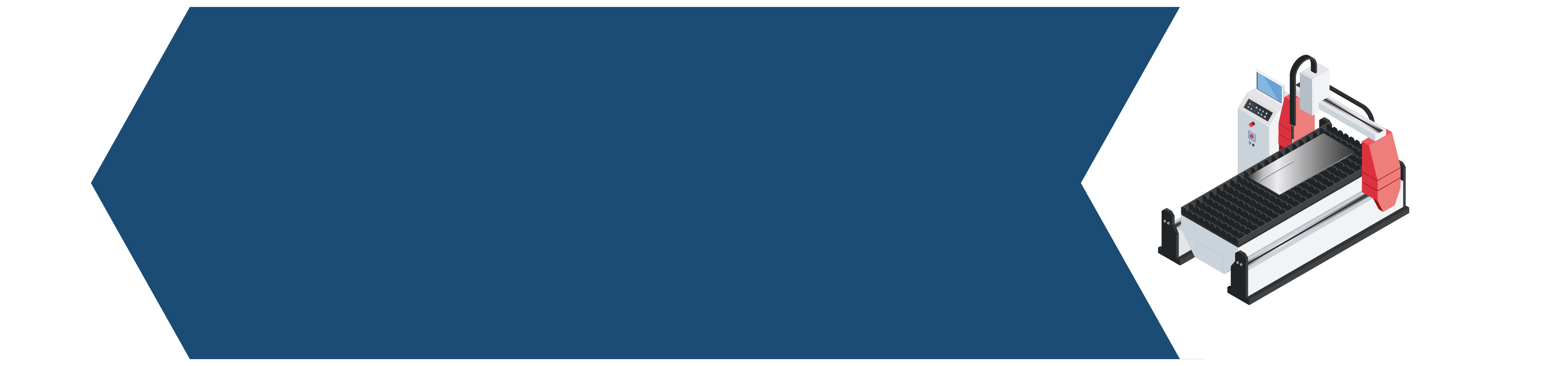
PRODUCTION & MANUFACTURING
Adjutant’s Production features automate manufacturing and assembly from start to finish. Production work orders list every part needed for assembly or fabrication based on a Bill of Materials with allocations and detailed inventory tracking. Scheduling and work order generation happens with a push of the button from the sales order.
Production Work Order Routing facilitates the scheduling and management of a production work-flow environment, managing the execution of a predetermined schedule and automatically updating the schedule based on set triggers. Inventory accounting is immediately created, both for work-in-process allocation and final assembly. Detailed reports offer a complete accounting picture of raw material costs and finished good inventory value.
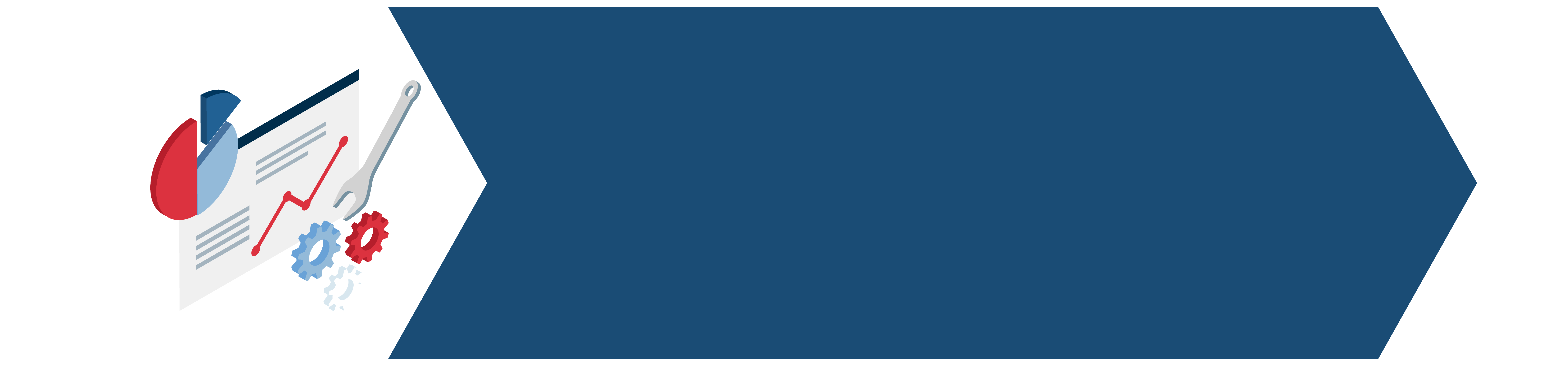
SHOP FLOOR CONTROL
The Shop Floor Control module in Adjutant is a powerful yet easy-to-use tool that gives you the ability to efficiently schedule your shop floor and utilize all your work centers to their most productive capacity. Access up-to-date information on the current activity in your shop, including job details and the order work needs to be performed in. Before committing to a schedule, quickly identify potential bottlenecks on the shop floor and compare the work committed against the shop floor’s ability to perform the work.
With Adjutant, you always know the status of a job on the floor - including production status, cost variables, and shipping schedules.
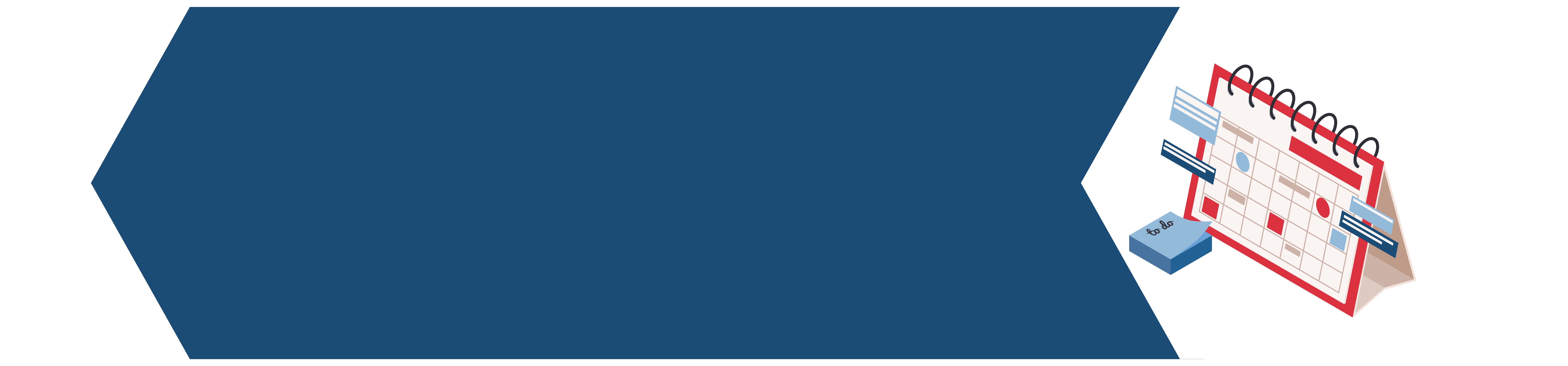
SHOP FLOOR ROUTING
Working in conjunction with the Production and Bill of Material modules, Adjutant’s Production Work Order Routing facilitates the scheduling and management of a production work-flow environment. It manages the execution of a predetermined schedule and automatically updates the schedule based on a combination of variables. Increase productivity, decrease costs, and receive better labor and material projections with the Routing module.
The Production Scheduling tool offers a way to manage all the production work orders in your shop with an on-screen display based on the production plant and due date. From one screen, you can quickly find orders using common filters - and reschedule, reprint, or change order details with just a few clicks.
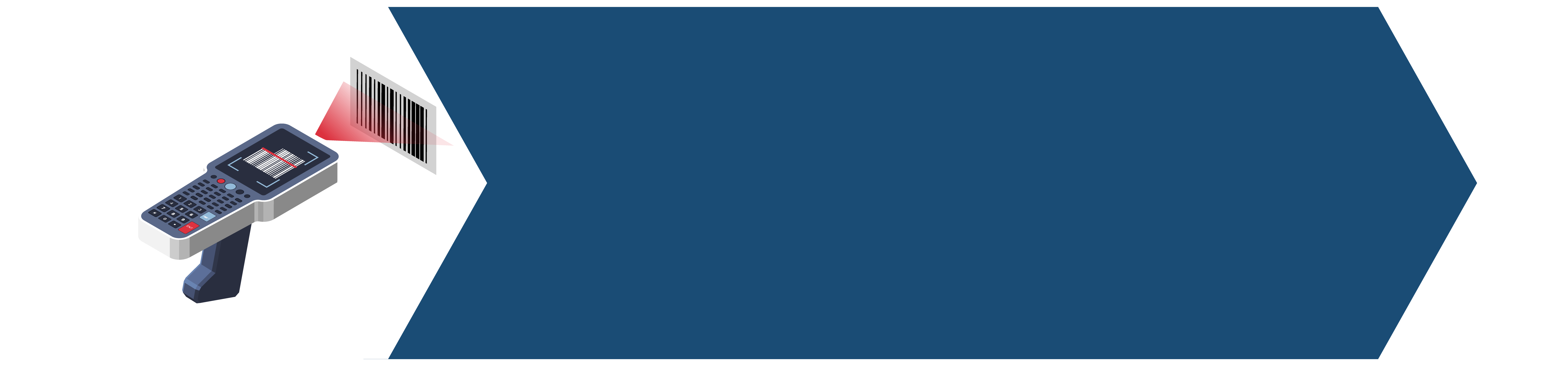
WIRELESS WAREHOUSE MANAGEMENT SYSTEM
Adjutant’s Wireless Warehouse Management System (WMS) utilizes incredibly stable wireless barcode technology and provides comprehensive, real-time visibility of every activity in your warehouse. This module handles receiving, put-away, picking, packing, and complete inventory management.
The WMS integrates with Adjutant’s Inventory Management system to allow inventory cycle counts to be created and sent directly to certain scanners so that the counters are assigned to exactly the inventory locations or items that they need to cover. The prompts on the scanners walk employees through the process, leaving little room for error. Scanners can also be used to check inventory levels, manage inventory locations, and produce inventory labels on-the-fly.
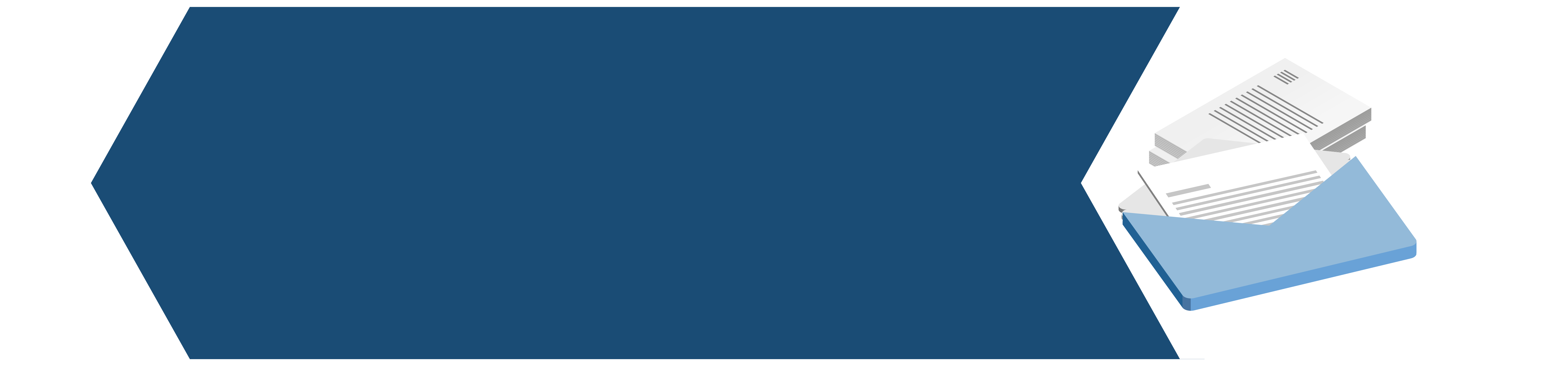
WORK ORDER MANAGEMENT
Adjutant’s Work Order Management module enables you to control your workflow by utilizing an efficient methodology to issue and assign work orders. It is the perfect tool to increase the performance of your in-house and mobile workforce.
Plan predetermined recurring tasks for preventative maintenance schedules or create and assign them on-the-fly as needed. Wireless connectivity gives you real-time visibility of mobile work-in-progress information and allows you to make better dispatch decisions. Seamless integration with other Adjutant modules gives your entire workforce immediate access to client and site information, contractual obligations, project information, and so much more!
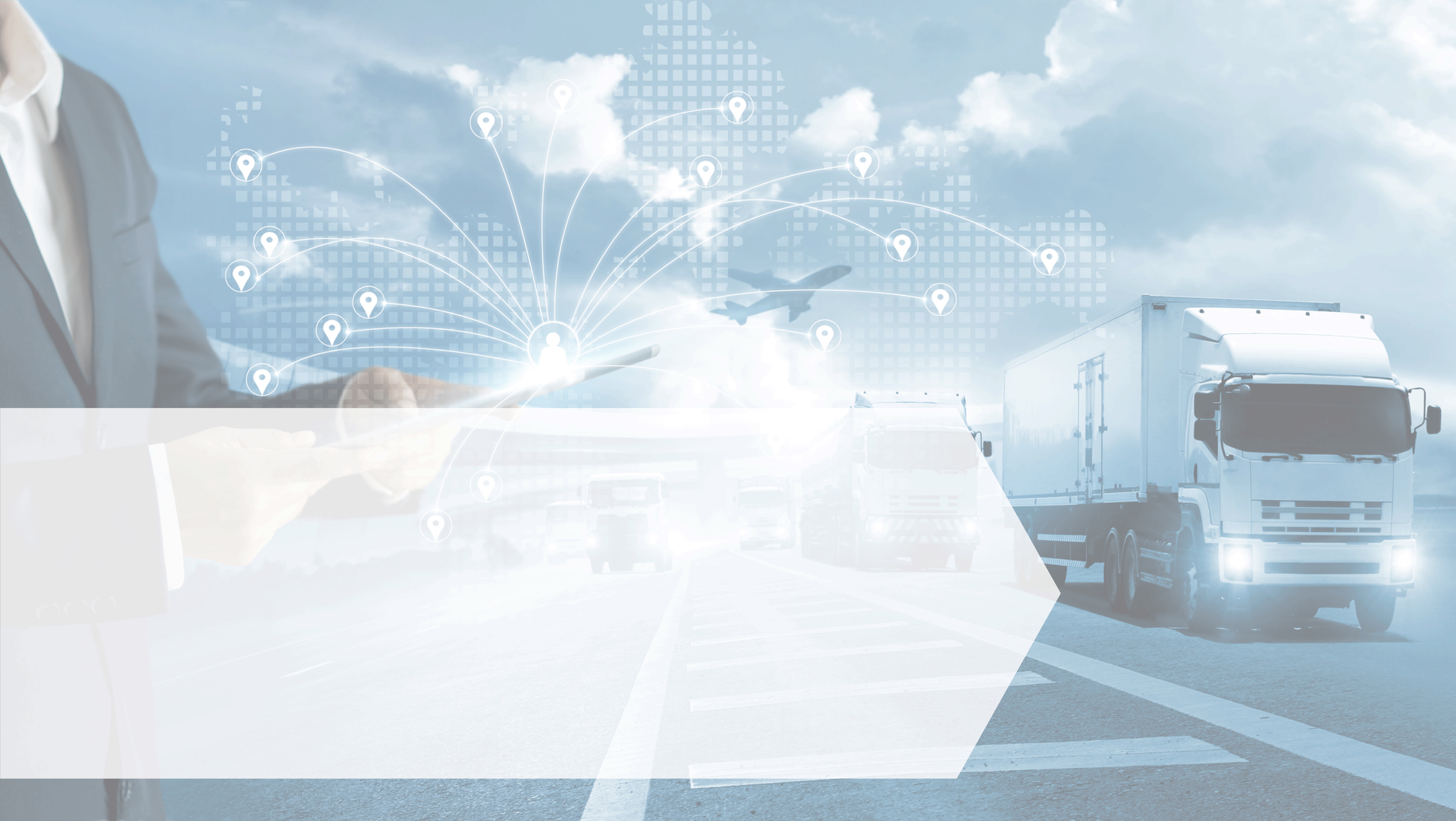
Adjutant’s Driver Delivery Portal has a mobile-friendly interface designed to work on any internet-connected mobile device and provides all the functions needed for professional deliveries in a compact and smart design.
Integration with Google Maps’ API helps route drivers intelligently through all scheduled deliveries. Drivers can use the mobile device camera to scan packages as they unload and mark them as delivered. Camera integration also allows drivers to take pictures of the delivery site that automatically link to the shipping record and are saved in the Document Vault. Managers back at the office can immediately see proof of delivery and be ready for customer inquiries. Drivers can capture a signature using an on-screen Bill of Lading for added liability control.
Drivers also have extra tools built into the portal to process damaged or rejected orders in real time. The customer information snapshot included provides drivers with comprehensive details about each customer’s outstanding orders so they can respond intelligently to any questions posed about pending orders. Best of all, as long as they are connected to the internet, all of the information is up-to-the-minute, and all actions are immediately shared with Adjutant for office personnel.
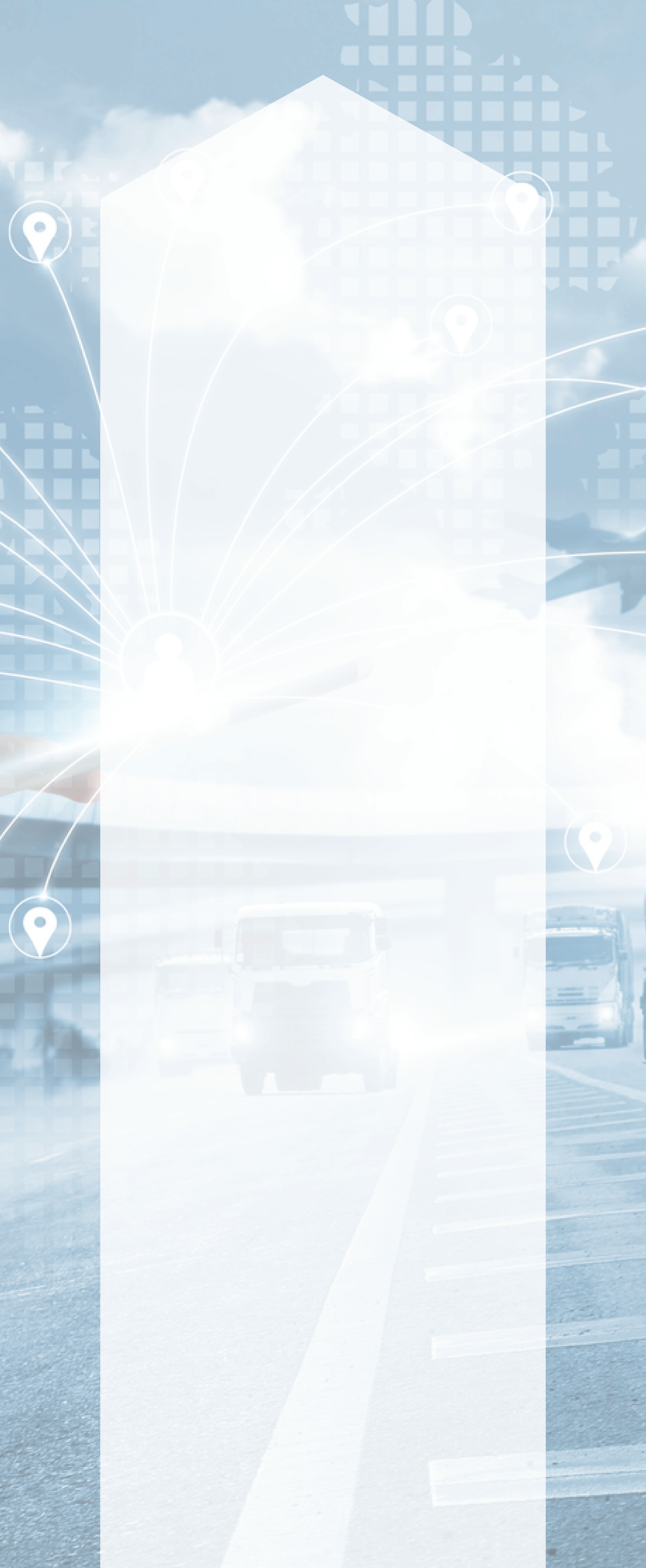
Adjutant’s Driver Delivery Portal has a mobile-friendly interface designed to work on any internet-connected mobile device and provides all the functions needed for professional deliveries in a compact and smart design.
Integration with Google Maps’ API helps route drivers intelligently through all scheduled deliveries. Drivers can use the mobile device camera to scan packages as they unload and mark them as delivered. Camera integration also allows drivers to take pictures of the delivery site that automatically link to the shipping record and are saved in the Document Vault. Managers back at the office can immediately see proof of delivery and be ready for customer inquiries. Drivers can capture a signature using an on-screen Bill of Lading for added liability control.
Drivers also have extra tools built into the portal to process damaged or rejected orders in real time. The customer information snapshot included provides drivers with comprehensive details about each customer’s outstanding orders so they can respond intelligently to any questions posed about pending orders. Best of all, as long as they are connected to the internet, all of the information is up-to-the-minute, and all actions are immediately shared with Adjutant for office personnel.
So… What If Your
Business Could Run Itself?
So… What If
Your Business
Could Run Itself?
Schedule a demo with us today, and see how
much of your time you can reclaim with
Adjutant Software Platform.
Schedule a demo with us today,
and see how much of your time
you can reclaim with the
Adjutant Software Platform.
About ABIS
ABIS was founded in 1983, and in the 40 years since, we have established our niche in the steel sector. Our team continues to build upon industry best practices to offer the most comprehensive, robust business process management software available – the Adjutant Software Platform. We’ve built ourselves on the premise that you shouldn’t need any more than one great software to effectively automate your operations, and we’re determined to spend the next 40 years continuing to make business smarter across North America.
Let Us Solve Your Headaches!
Contact Info
At ABIS, we welcome the opportunity to speak to discuss how we can help equip your business with the tools it needs to succeed. Our solutions are built by our team and tailored for your industry.
Please provide your contact information and we will reach out to you as soon as possible. We look forward to hearing from you!
1415 North Loop West, Suite 1200
Houston, TX 77008 713-680-2247 info@abiscorp.com