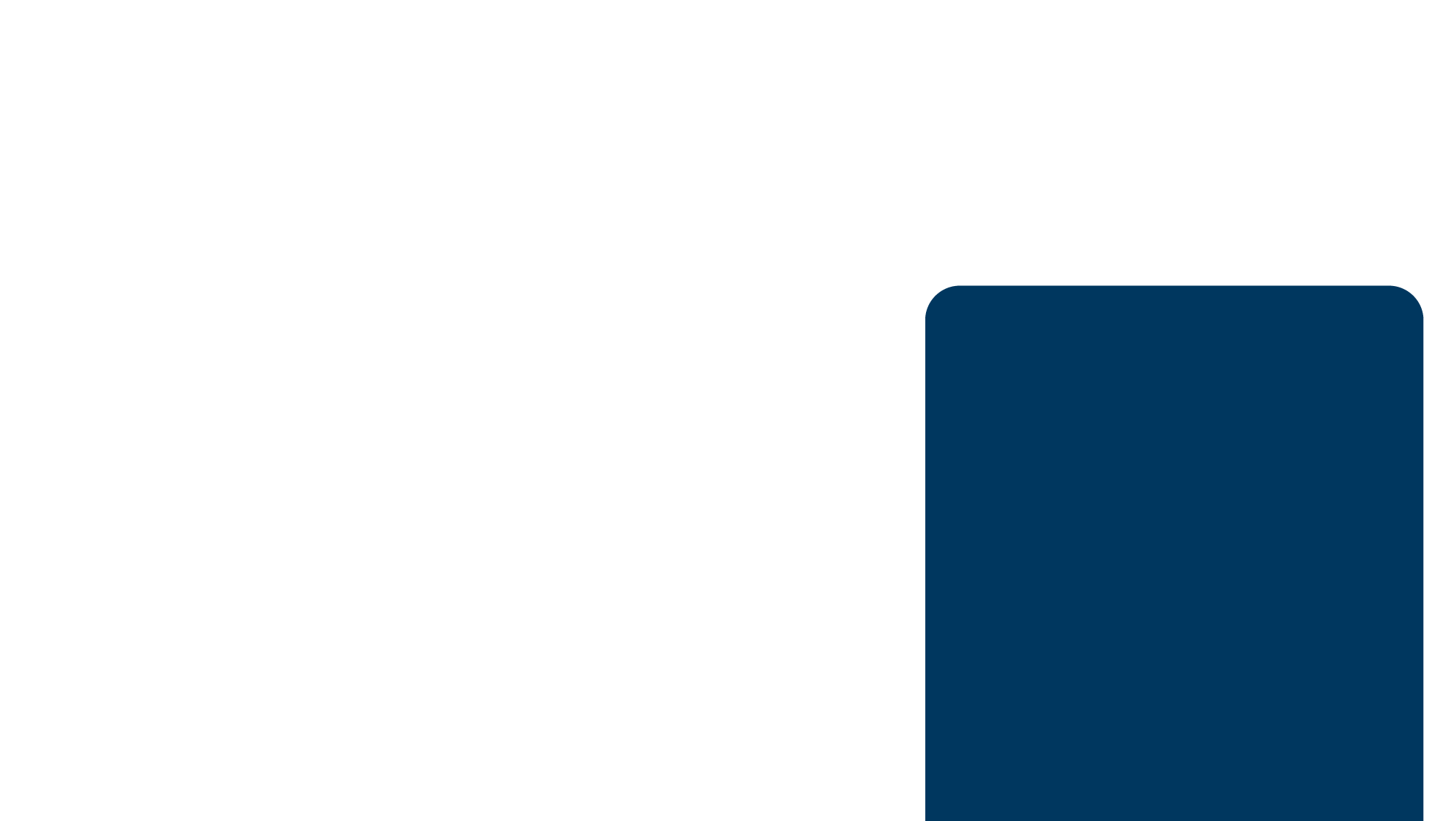
• Metal Stamping
• Field Erection
• Slitting
• Shearing
• Metal Punching
• Pole Barns
• Metal Finishing
• Metal Casting
• Machining & Welding
• Steel Fabrication
• Metal Heat Treating
• Metal & Powder Coating
• Metal Structures & Metal Framing
• Metal Cutting
• Metal Bending
• Wire Rolling & Forming
• Metal Processing & Metal Extrusions
• Coil, Plate, & Bar Processing
• Metal Roofing & Siding
• Metal Building Systems
and see how Adjutant fits into your business!
Don't see what you do listed here?
Of Growing Your Business
We're In The Business
Reach Out To Us

We're In The Business
Of Growing Your Business
• Metal Building Systems
• Metal Roofing & Siding
• Coil, Plate, & Bar Processing
• Metal Processing & Metal Extrusions
• Wire Rolling & Forming
• Metal Bending
• Metal Cutting
• Metal Structures & Metal Framing
• Metal & Powder Coating
• Metal Heat Treating
• Steel Fabrication
• Machining & Welding
• Metal Casting
• Metal Finishing
• Pole Barns
• Metal Punching
• Shearing
• Slitting
• Field Erection
• Metal Stamping
Don't see what you do listed here?
Reach Out To Us
and see how Adjutant fits into your business!
Features For Your Industry
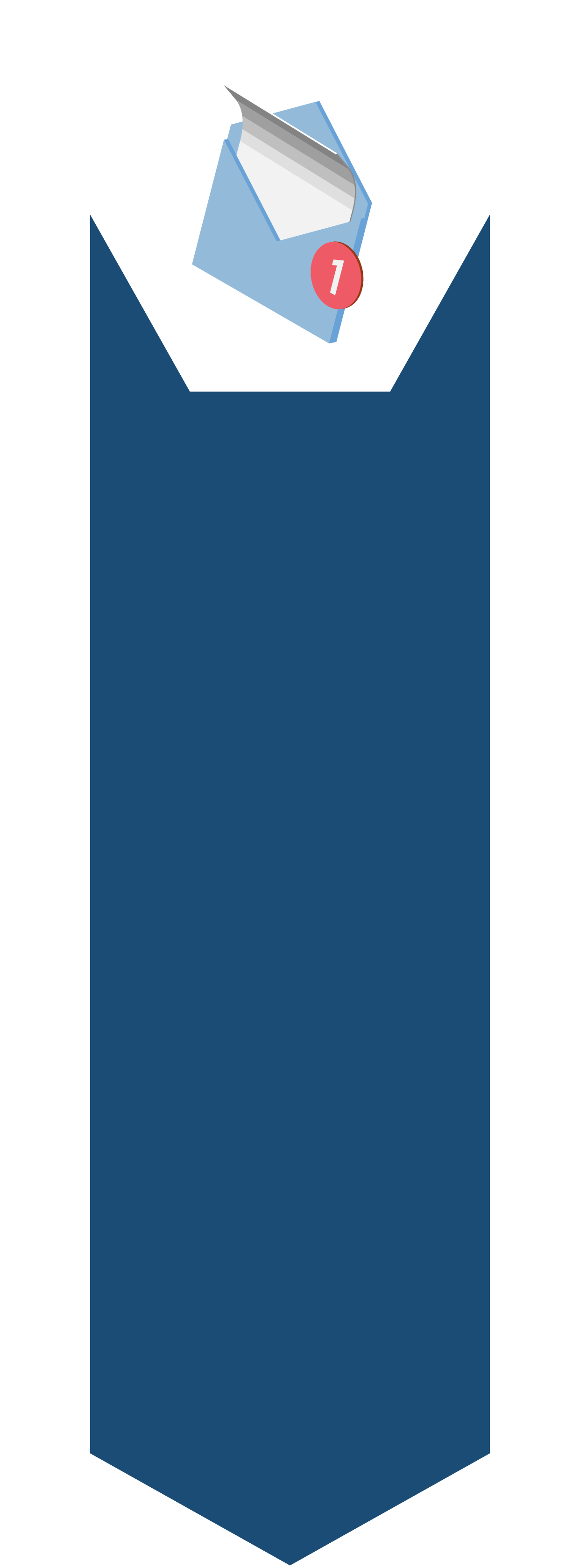
AUTO ALERT
Adjutant's Auto Alert feature is a sophisticated alerts system that automates the notification of employees, customers, and others of critical events as they happen. It provides valuable information the instant you need it and enables you to focus on important events as defined by you. Auto Alert enables companies to meet deadlines and service level agreements by keeping customers and employees informed with necessary real-time information.
The Auto Alert system is integrated with your email system to deliver rich-content, event-based emails directly to your customer from your company's email domain. Alert emails can be customized using our Email Template applications to include your company logo, graphics, contact, details, web links to company resources, and even links to Adjutant records.
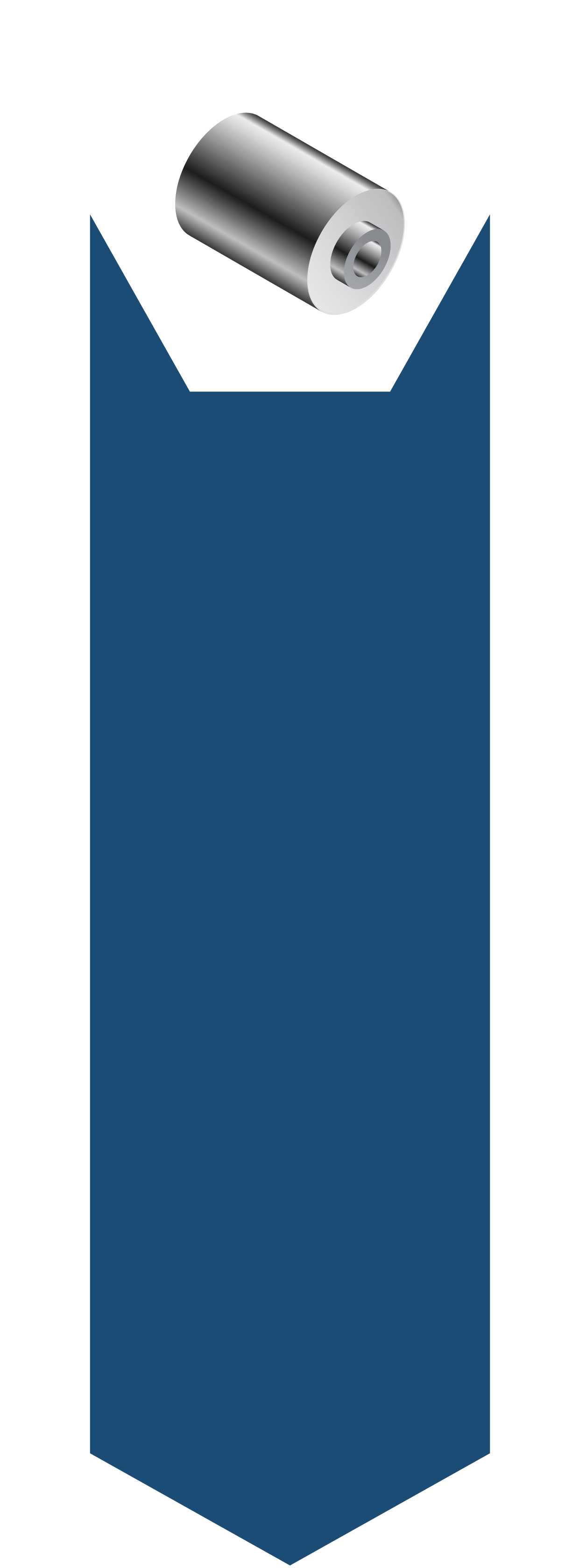
COIL TAGGING & TRACKING
Adjutant's Coil Tracking features automate this time-consuming and paper-heavy process. Coils are assigned a special item attribute that prompts special reflexes throughout Adjutant which are unique to coil material. Receiving coil triggers special prompts and coil tag printing. Coils are simultaneously tracked in both pounds and lineal feet, and a separate cost per unit is stored for each. This built-in flexibility allows for deeper analysis of costs and additional reporting options.
Document Imaging allows documents to be stored either with the original purchase order or directly with each unique coil. Each coil can have its own Document Vault that contains the critical files, such as MTR's, and documents available to review with the click of a mouse. You get visibility into the entire life cycle of a coil, from its purchase to the last job it was used for.
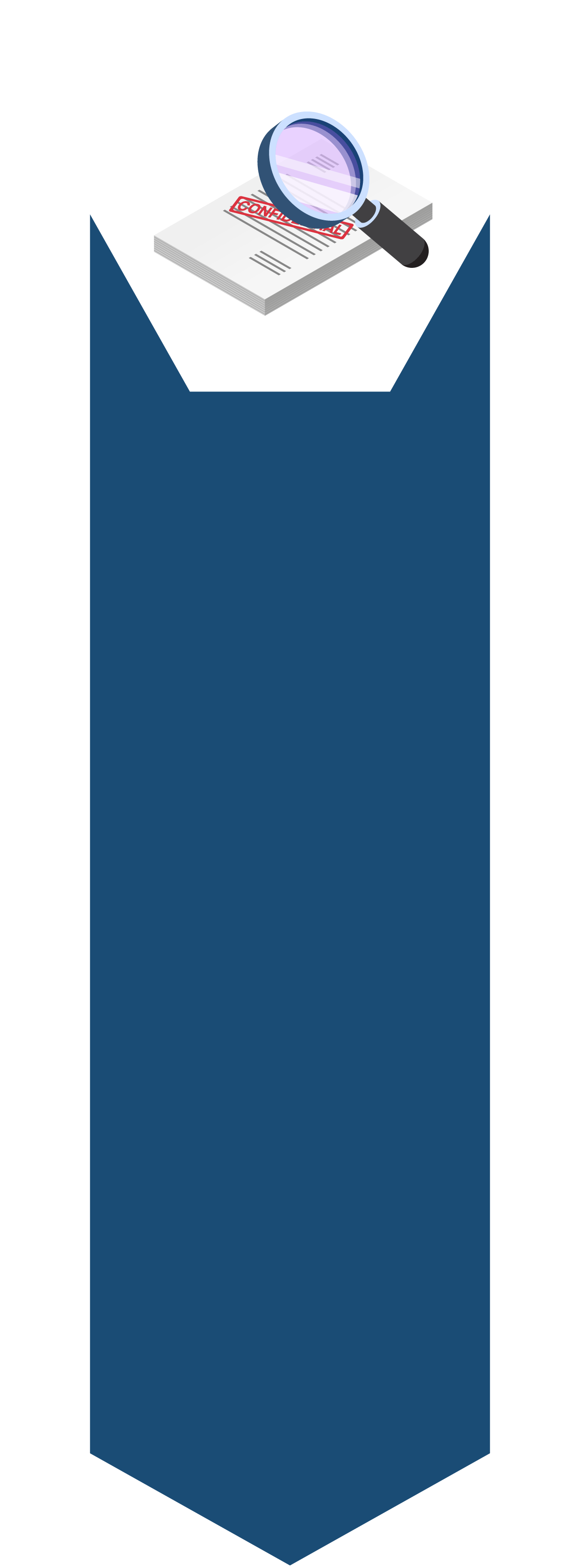
DOCUMENT IMAGING
Adjutant’s Document Imaging provides organizations with a scalable solution focused on storing images and documents where you need them. The Document Imaging module creates Document Vaults for almost every record in the Adjutant Software Platform. Each record inside of each application has a dedicated vault to store documents and images that can be instantly viewed and reproduced by anyone in your organization with the proper security access.
The Document Imaging system also offers process automation with easy-to-use email tags that let you forward file attachments directly to a specific record’s Document Vault. Adjutant uses a dedicated email account that ties directly to the Document Imaging system and saves file attachments right where you need them.
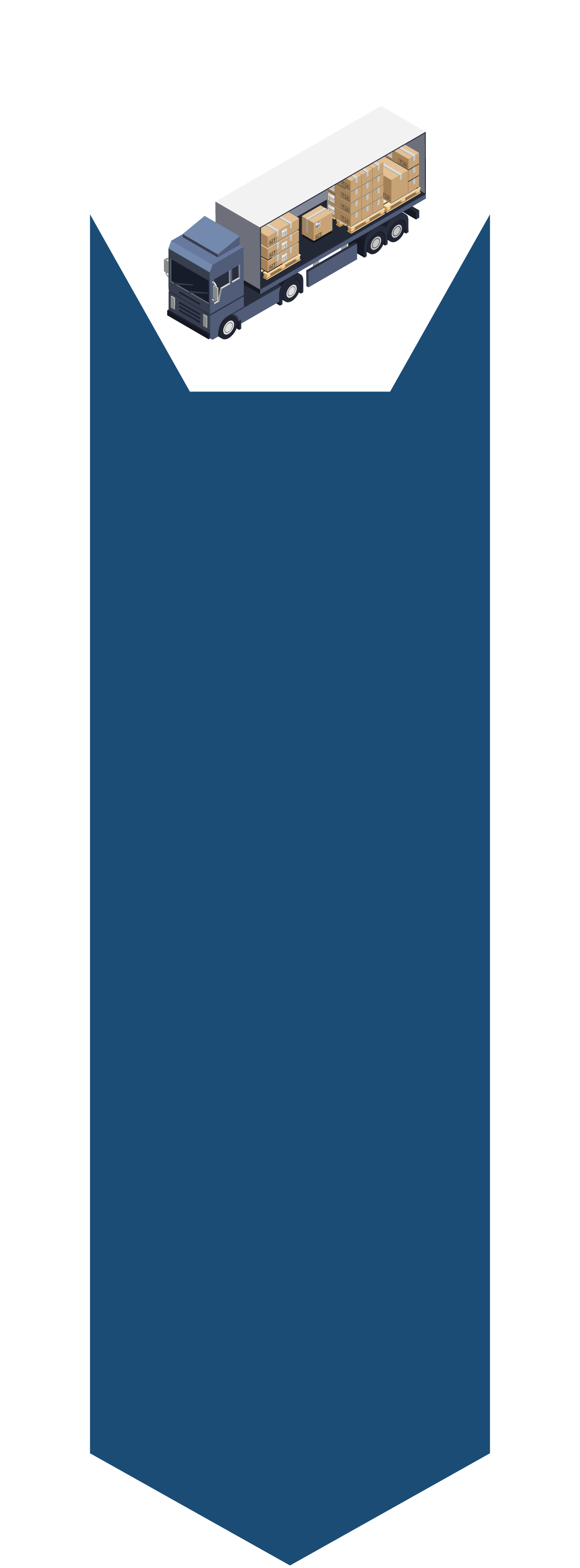
LOGISTICS
The Shipping Events module gives your shipping department complete control over pending shipments. The tools available with Adjutant Shipping Events provide maximum visibility of your packing, loading, and shipping operations from start to finish. Shipping Events is deeply integrated with the inventory, sales, and production modules so you are always notified during the shipping process of any issues with inventory levels or items that are not ready to load. Shipping details are shared between the integrated applications, so it is always easy to drill-down from sales orders or inventory screens to find the shipping record from almost any starting point. Shipping Events’ integration with other powerful features like Document Imaging, Bills of Lading, Delivery Routes, and Wireless Warehouse can streamline or modernize your shipping operations, increasing employee productivity and customer satisfaction.
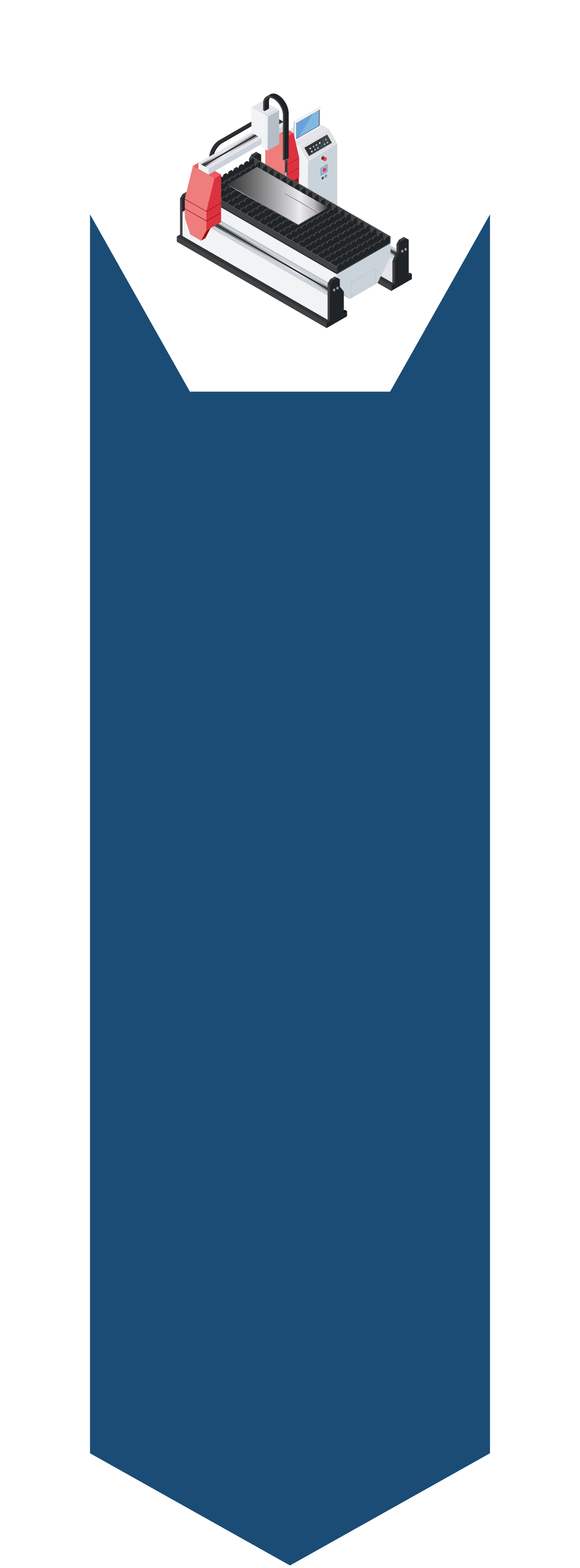
PRODUCTION
Adjutant’s Production features automate manufacturing and assembly from start to finish. Production work orders list every part needed for assembly or fabrication based on a Bill of Materials with allocations and detailed inventory tracking. Scheduling and work order generation happens with a push of the button from the sales order.
Production Work Order Routing facilitates the scheduling and management of a production work-flow environment, managing the execution of a predetermined schedule and automatically updating the schedule based on set triggers. Inventory accounting is immediately created, both for work-in-process allocation and final assembly. Detailed reports offer a complete accounting picture of raw material costs and finished good inventory value.
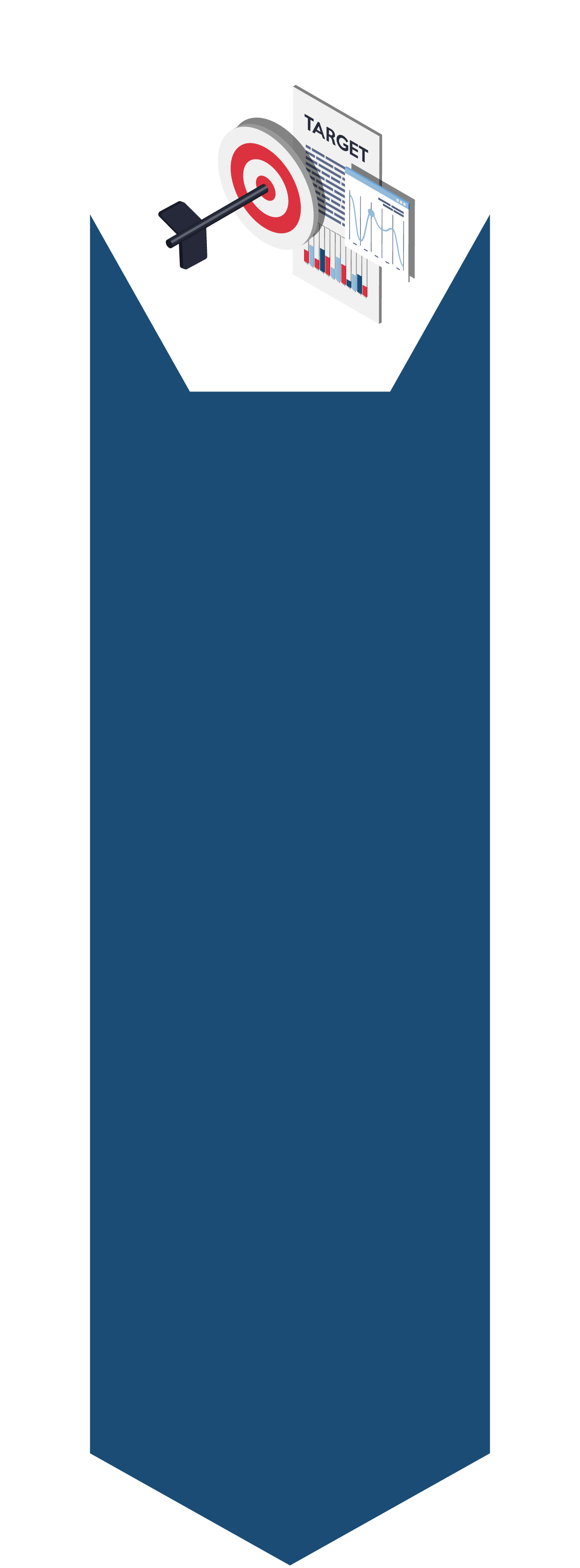
PROJECT MANAGEMENT
Adjutant’s Project Management tracks key details from every sales order, purchase order, production work order, shipping event and carton, and even tasks, invoices, and payables. Project Phases let you define distinct project stages that can be tied to the orders and tasks linked to a project. This lets you control the different dates related to each phase, as well as set the budget and financial benchmarks for each stage.
With every system tied together, you can see all related costs in one place on the Project Job Cost tab in each project record. This allows you to quickly verify whether the project is on track to be profitable, and make adjustments as soon as possible. The Project Grid lets you manage all of your projects from one location and stay on top of changes as they happen.
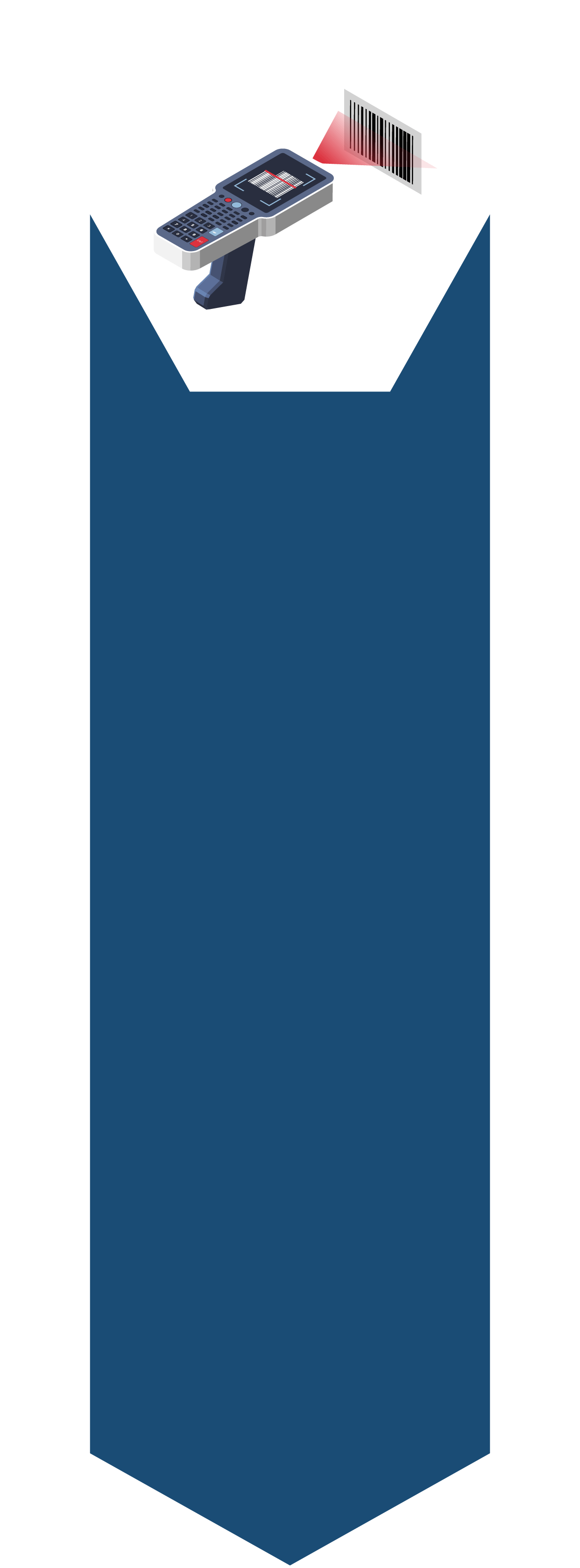
WIRELESS WMS
Adjutant’s Wireless Warehouse Management System (WMS) utilizes incredibly stable wireless barcode technology and provides comprehensive, real-time visibility of every activity in your warehouse. This module handles receiving, put-away, picking, packing, and complete inventory management.
The WMS integrates with Adjutant’s Inventory Management system to allow inventory cycle counts to be created and sent directly to certain scanners so that the counters are assigned to exactly the inventory locations or items that they need to cover. The prompts on the scanners walk employees through the process, leaving little room for error. Scanners can also be used to check inventory levels, manage inventory locations, and produce inventory labels on-the-fly.
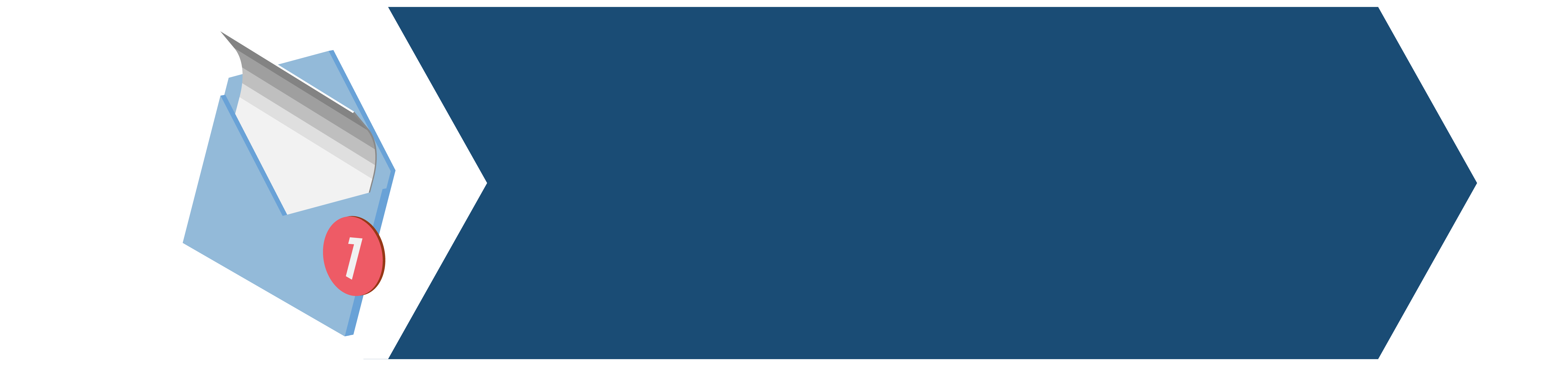
AUTO ALERT
Adjutant's Auto Alert feature is a sophisticated alerts system that automates the notification of employees, customers, and others of critical events as they happen. It provides valuable information the instant you need it and enables you to focus on important events as defined by you. Auto Alert enables companies to meet deadlines and service level agreements by keeping customers and employees informed with necessary real-time information.
The Auto Alert system is integrated with your email system to deliver rich-content, event-based emails directly to your customer from your company's email domain. Alert emails can be customized using our Email Template applications to include your company logo, graphics, contact, details, web links to company resources, and even links to Adjutant records.
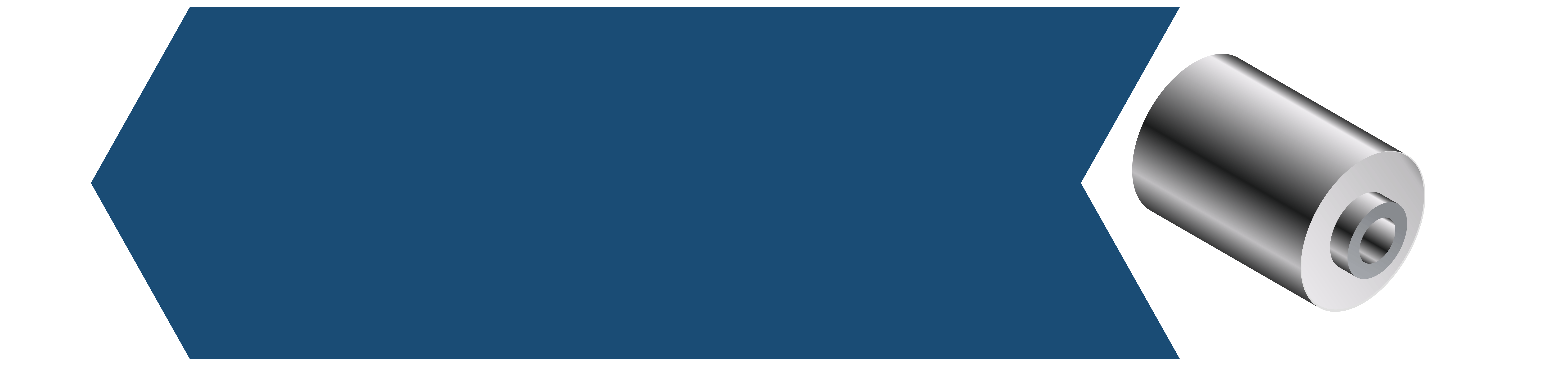
COIL TAGGING AND TRACKING
Adjutant's Coil Tracking features automate this time-consuming and paper-heavy process. Coils are assigned a special item attribute that prompts special reflexes throughout Adjutant which are unique to coil material. Receiving coil triggers special prompts and coil tag printing. Coils are simultaneously tracked in both pounds and lineal feet, and a separate cost per unit is stored for each. This built-in flexibility allows for deeper analysis of costs and additional reporting options.
Document Imaging allows documents to be stored either with the original purchase order or directly with each unique coil. Each coil can have its own Document Vault that contains the critical files, such as MTR's, and documents available to review with the click of a mouse. You get visibility into the entire life cycle of a coil, from its purchase to the last job it was used for.
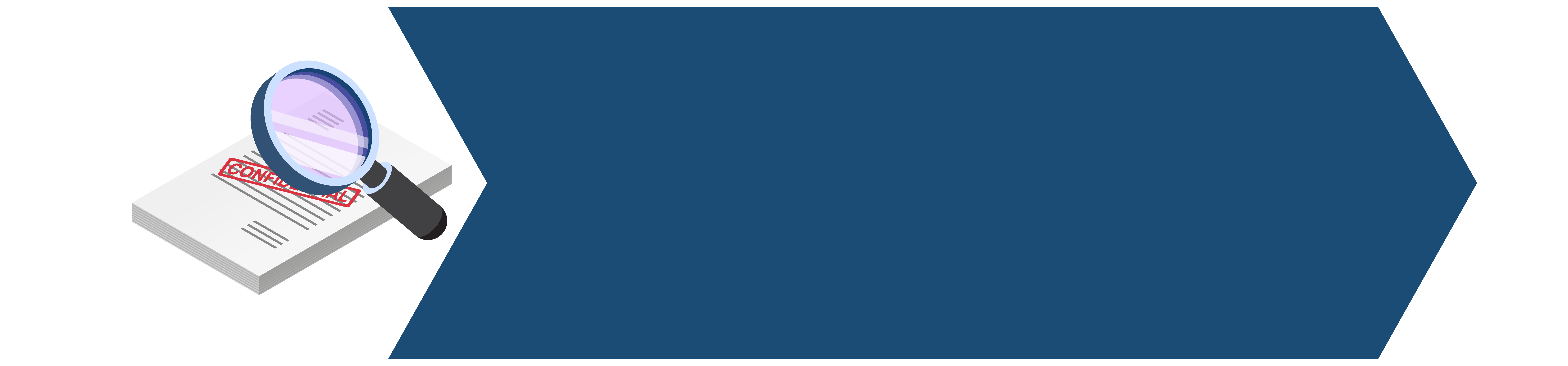
DOCUMENT IMAGING
Adjutant’s Document Imaging provides organizations with a scalable solution focused on storing images and documents where you need them. The Document Imaging module creates Document Vaults for almost every record in the Adjutant Software Platform. Each record inside of each application has a dedicated vault to store documents and images that can be instantly viewed and reproduced by anyone in your organization with the proper security access.
The Document Imaging system also offers process automation with easy-to-use email tags that let you forward file attachments directly to a specific record’s Document Vault. Adjutant uses a dedicated email account that ties directly to the Document Imaging system and saves file attachments right where you need them.
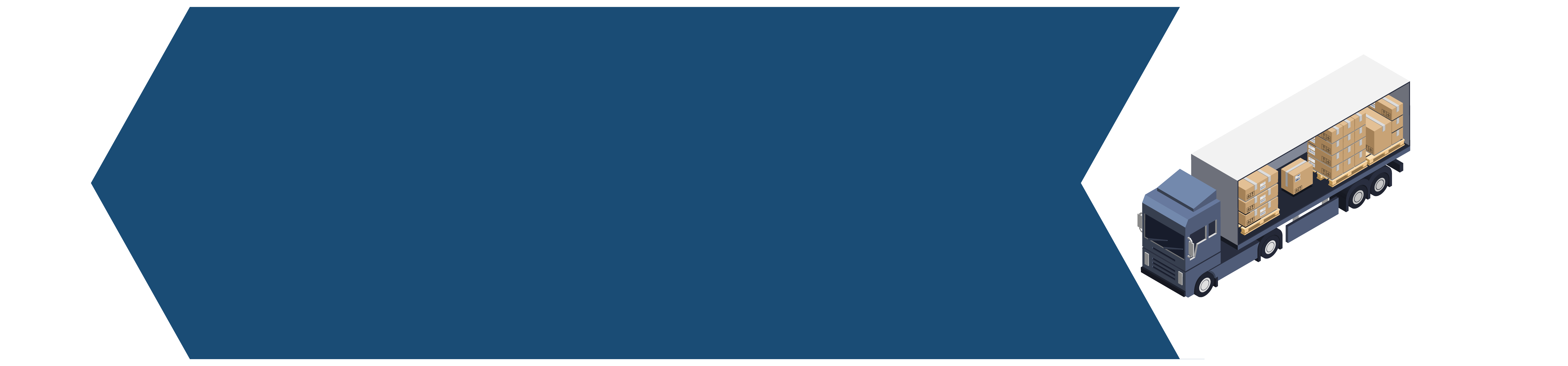
LOGISTICS - SHIPPING EVENTS
The Shipping Events module gives your shipping department complete control over pending shipments. The tools available with Adjutant Shipping Events provide maximum visibility of your packing, loading, and shipping operations from start to finish. Shipping Events is deeply integrated with the inventory, sales, and production modules so you are always notified during the shipping process of any issues with inventory levels or items that are not ready to load. Shipping details are shared between the integrated applications, so it is always easy to drill-down from sales orders or inventory screens to find the shipping record from almost any starting point. Shipping Events’ integration with other powerful features like Document Imaging, Bills of Lading, Delivery Routes, and Wireless Warehouse can streamline or modernize your shipping operations, increasing employee productivity and customer satisfaction.
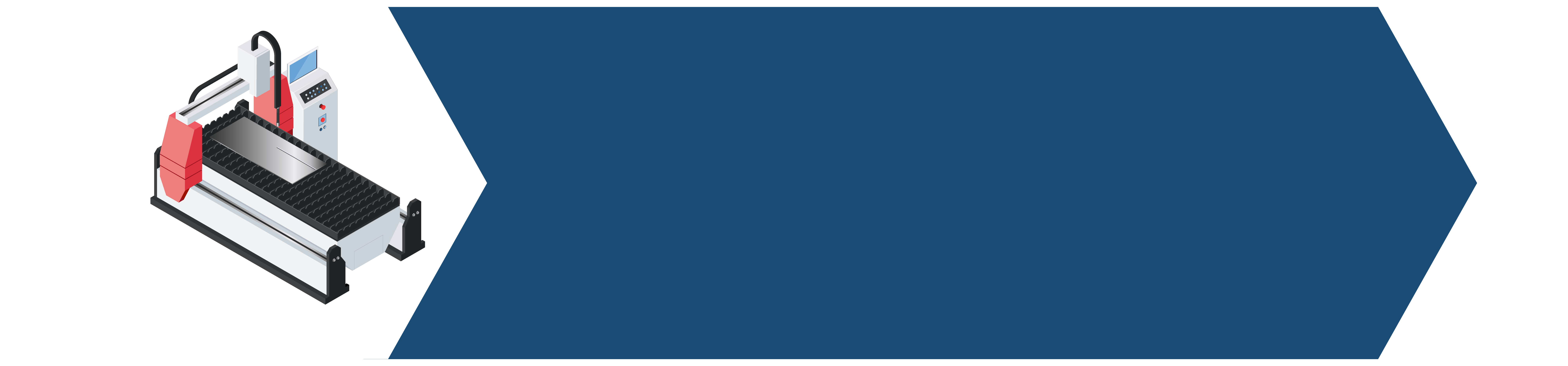
PRODUCTION
Adjutant’s Production features automate manufacturing and assembly from start to finish. Production work orders list every part needed for assembly or fabrication based on a Bill of Materials with allocations and detailed inventory tracking. Scheduling and work order generation happens with a push of the button from the sales order.
Production Work Order Routing facilitates the scheduling and management of a production work-flow environment, managing the execution of a predetermined schedule and automatically updating the schedule based on set triggers. Inventory accounting is immediately created, both for work-in-process allocation and final assembly. Detailed reports offer a complete accounting picture of raw material costs and finished good inventory value.
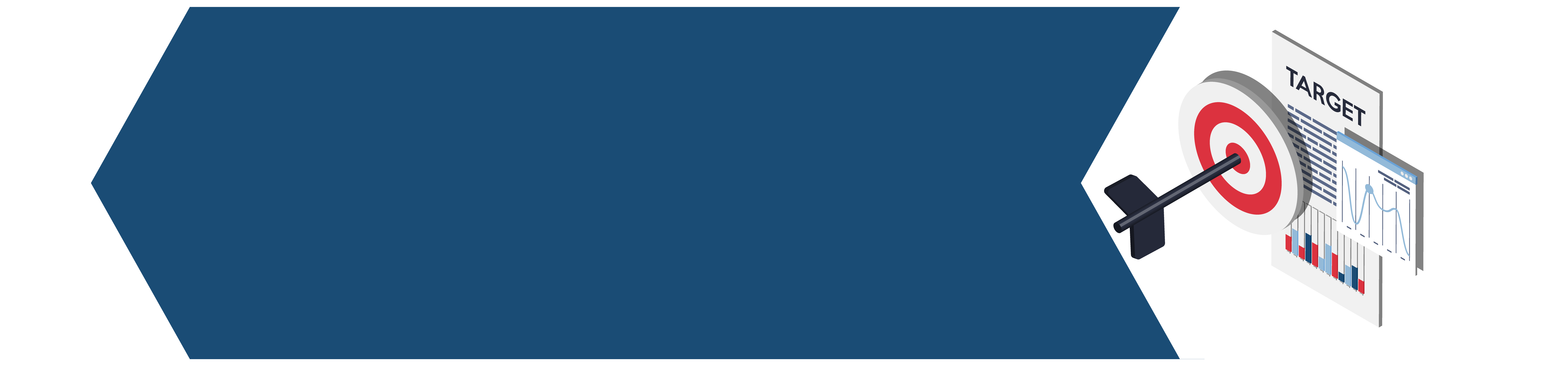
PROJECT MANAGEMENT
Adjutant’s Project Management tracks key details from every sales order, purchase order, production work order, shipping event and carton, and even tasks, invoices, and payables. Project Phases let you define distinct project stages that can be tied to the orders and tasks linked to a project. This lets you control the different dates related to each phase, as well as set the budget and financial benchmarks for each stage.
With every system tied together, you can see all related costs in one place on the Project Job Cost tab in each project record. This allows you to quickly verify whether the project is on track to be profitable, and make adjustments as soon as possible. The Project Grid lets you manage all of your projects from one location and stay on top of changes as they happen.
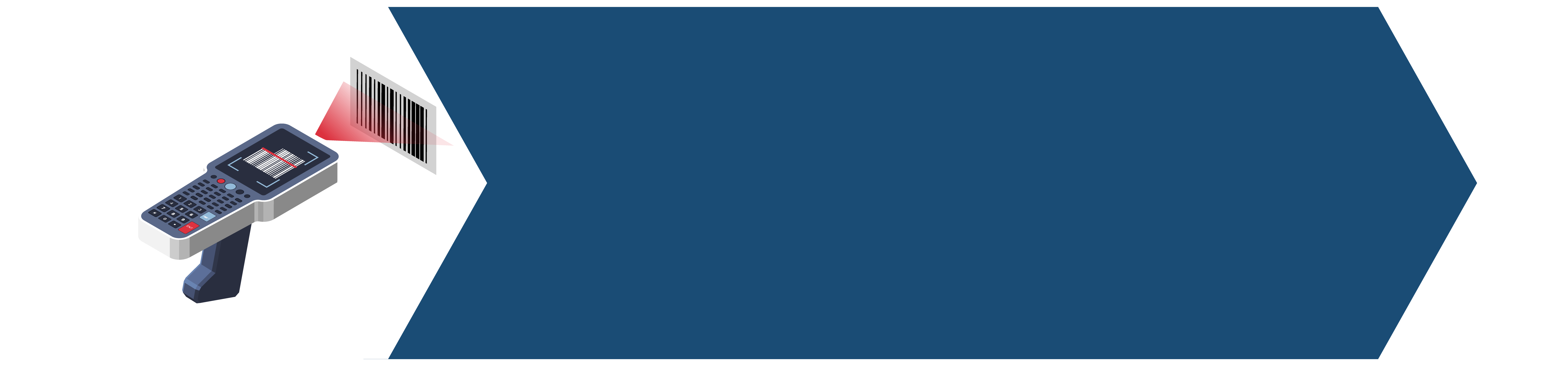
WIRELESS WAREHOUSE MANAGEMENT SYSTEM
Adjutant’s Wireless Warehouse Management System (WMS) utilizes incredibly stable wireless barcode technology and provides comprehensive, real-time visibility of every activity in your warehouse. This module handles receiving, put-away, picking, packing, and complete inventory management.
The WMS integrates with Adjutant’s Inventory Management system to allow inventory cycle counts to be created and sent directly to certain scanners so that the counters are assigned to exactly the inventory locations or items that they need to cover. The prompts on the scanners walk employees through the process, leaving little room for error. Scanners can also be used to check inventory levels, manage inventory locations, and produce inventory labels on-the-fly.
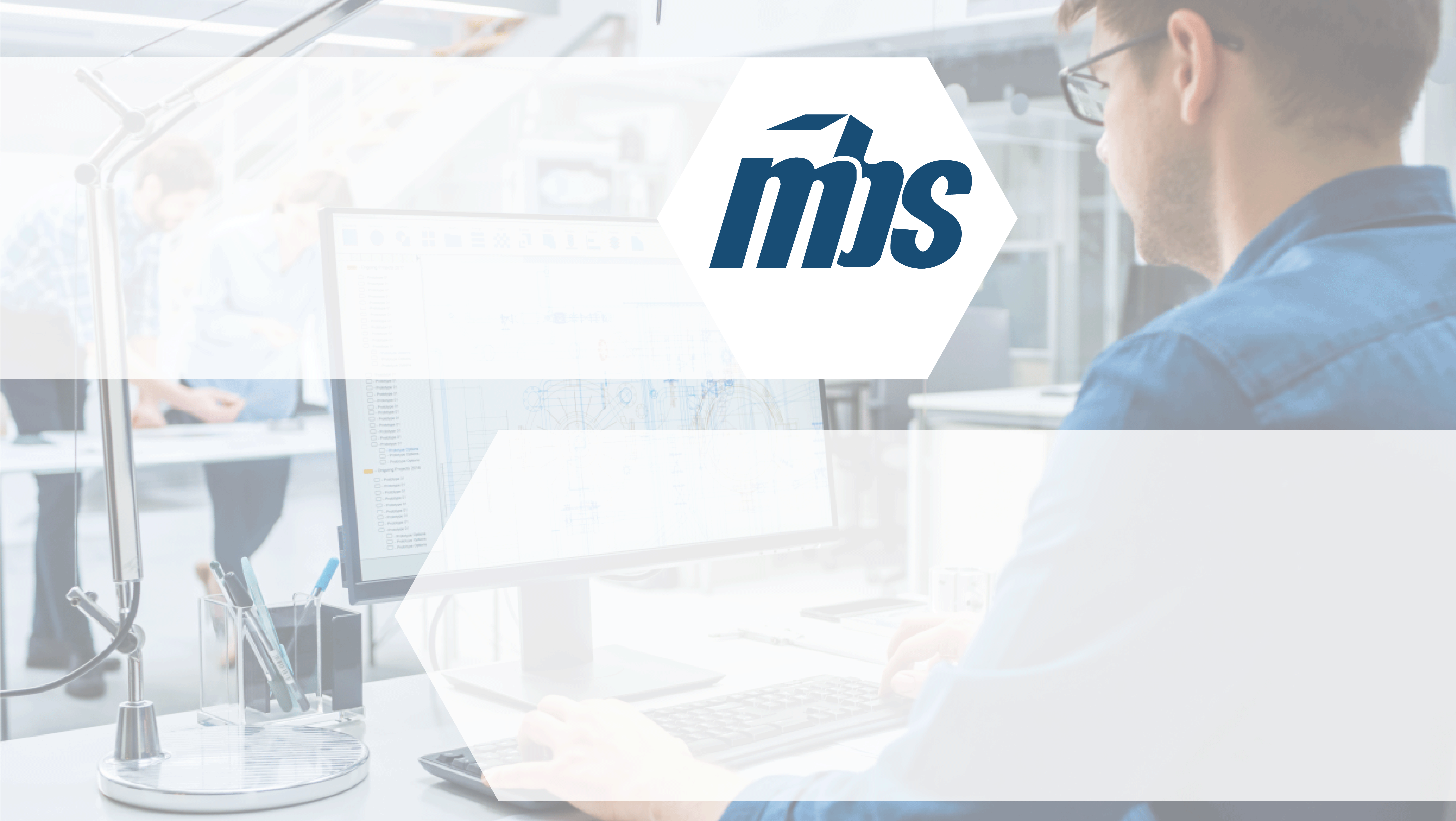
Our Engineering Software Integration module has been designed to import a Bill of Material (BOM) file directly from your CAD software. The import process links the BOM file to a specific sales order in Adjutant, creates the order, and ties the BOM order directly to your customer’s specific building project. Adjutant uses as an item code match-up system that learns as you go, meaning the import process gets faster and easier the more you use it.
Adjutant has worked with Metal Building Software files for years and have added functionality to allow a great amount of detail and configuration information to flow directly from MBS into your final production orders - keeping your orders accurate and avoiding costly mistakes.
Revolutionize your metal building production with Adjutant - automated integration, error-free, and future-proof.
Furthermore, with an aging workforce, the reliance on tribal knowledge can become a significant challenge. Our ERP platform addresses this issue by providing a standardized and streamlined approach to production processes, eliminating the need for tribal knowledge and reducing the risk of knowledge loss due to employee turnover. With our integrated approach, you can ensure that your production processes are not dependent on the expertise of a few individuals, but rather are based on a standardized and documented approach that can be easily replicated and followed by all employees.
Our platform provides more than just automated integration with roll-forming machines. By eliminating the need for manual data entry, our system not only reduces the risk of human error but also frees up valuable labor hours that can be allocated to more critical tasks. This results in a more efficient use of your workforce, reducing production costs and increasing overall productivity.
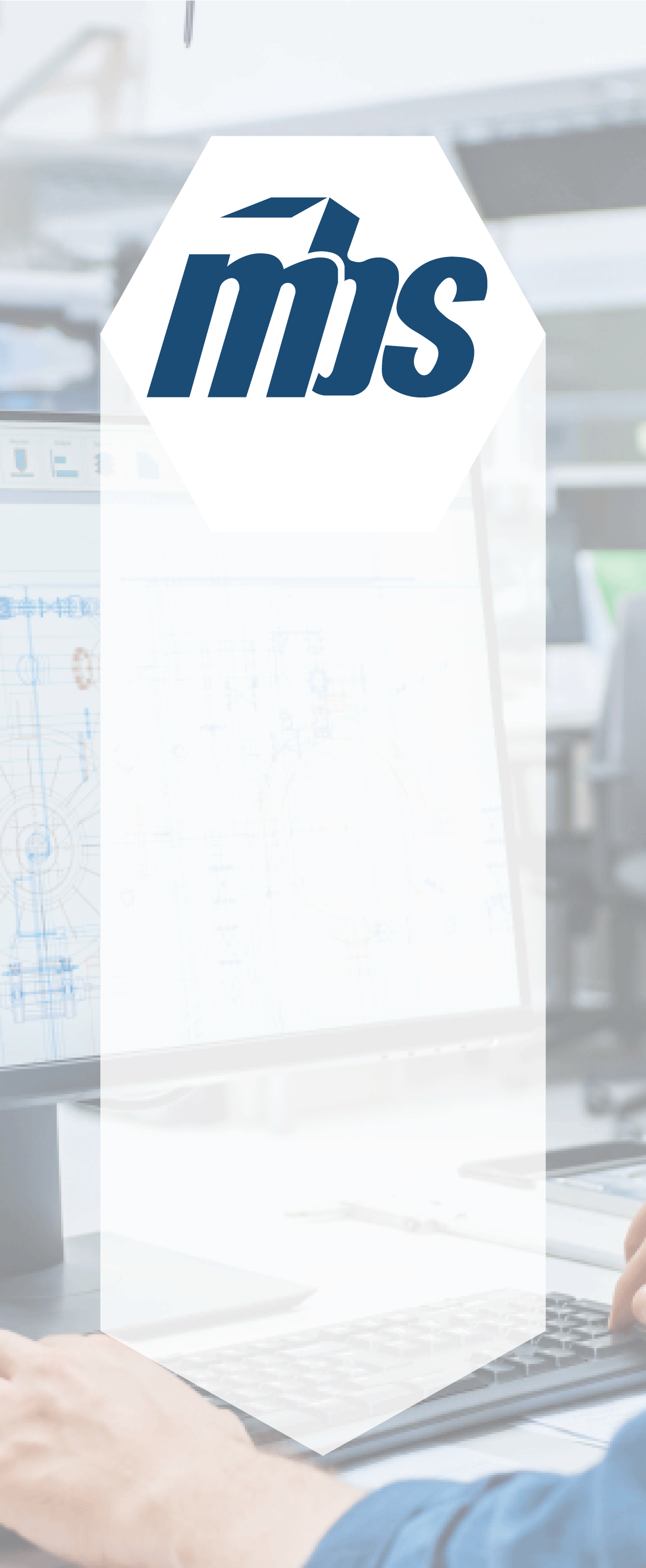
Our Engineering Software Integration module has been designed to import a Bill of Material (BOM) file directly from your CAD software. The import process links the BOM file to a specific sales order in Adjutant, creates the order, and ties the BOM order directly to your customer’s specific building project. Adjutant uses as an item code match-up system that learns as you go, meaning the import process gets faster and easier the more you use it.
Adjutant has worked with Metal Building Software files for years and have added functionality to allow a great amount of detail and configuration information to flow directly from MBS into your final production orders - keeping your orders accurate and avoiding costly mistakes.
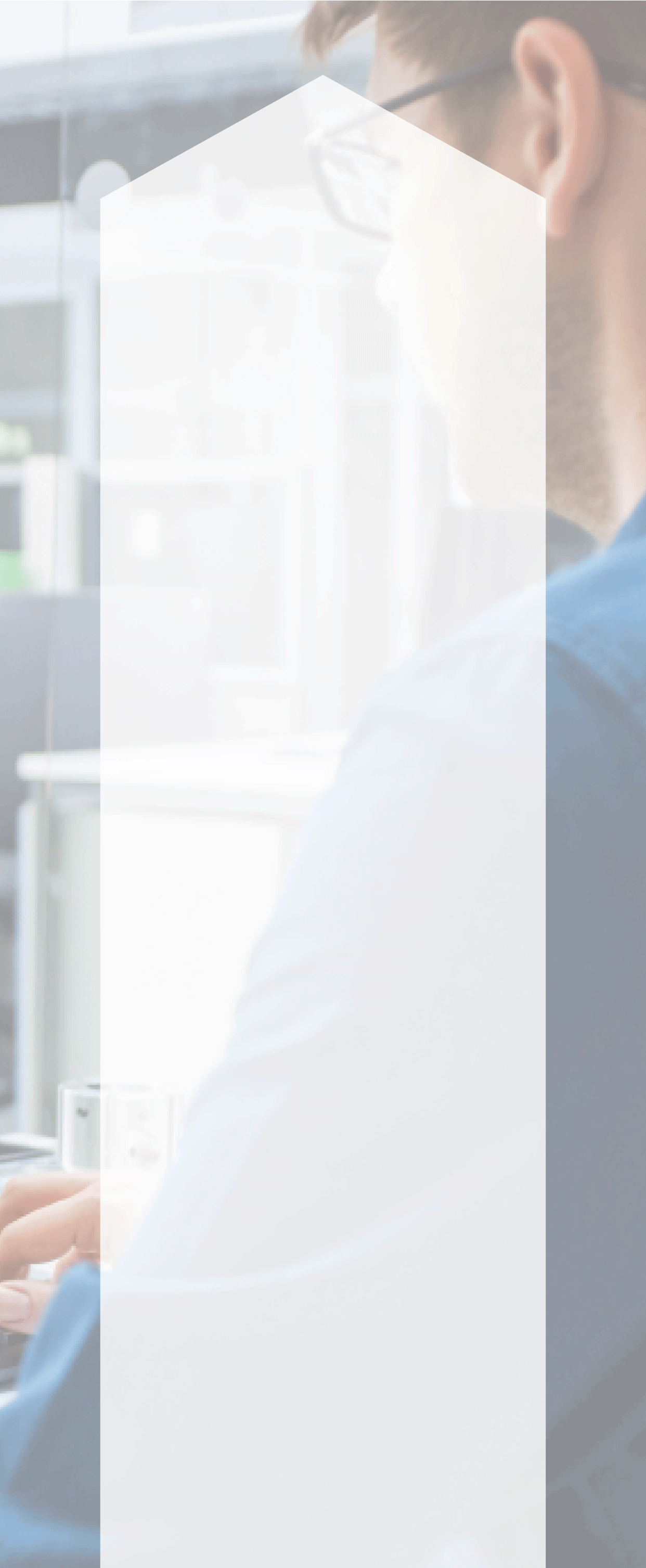
Our platform provides more than just automated integration with roll-forming machines. By eliminating the need for manual data entry, our system not only reduces the risk of human error but also frees up valuable labor hours that can be allocated to more critical tasks. This results in a more efficient use of your workforce, reducing production costs and increasing overall productivity.
Furthermore, with an aging workforce, the reliance on tribal knowledge can become a significant challenge. Our ERP platform addresses this issue by providing a standardized and streamlined approach to production processes, eliminating the need for tribal knowledge and reducing the risk of knowledge loss due to employee turnover. With our integrated approach, you can ensure that your production processes are not dependent on the expertise of a few individuals, but rather are based on a standardized and documented approach that can be easily replicated and followed by all employees.
Revolutionize your metal building production with Adjutant - automated integration, error-free, and future-proof.
So… What If Your
Business Could Run Itself?
So… What If
Your Business
Could Run Itself?
Schedule a demo with us today, and see how
much of your time you can reclaim with the
Adjutant Software Platform.
Schedule a demo with us today,
and see how much of your time
you can reclaim with the
Adjutant Software Platform.
About ABIS
ABIS was founded in 1983, and in the 40 years since, we have established our niche in the steel sector. Our team continues to build upon industry best practices to offer the most comprehensive, robust business process management software available – the Adjutant Software Platform. We’ve built ourselves on the premise that you shouldn’t need any more than one great software to effectively automate your operations, and we’re determined to spend the next 40 years continuing to make business smarter across North America.
Let Us Solve Your Headaches!
Contact Info
At ABIS, we welcome the opportunity to speak to discuss how we can help equip your business with the tools it needs to succeed. Our solutions are built by our team and tailored for your industry.
Please provide your contact information and we will reach out to you as soon as possible. We look forward to hearing from you!
1415 North Loop West, Suite 1200
Houston, TX 77008 713-680-2247 info@abiscorp.com